Crack detection
Detect microcracks reliably, automatically and non-destructively with the QASS measuring system
Real-time, in-line & production-ready
The permanent and force-fit connection of the QASS structure-borne sound sensor to the machine, enables the Optimizer4D to seamlessly monitor your straightening process. The data is processed and evaluated in real time.
Minimization of scrap
Fast processing of measurement data in real time: 3 million samples per second, spectral processing using Fourier transform, as well as noise reduction with adaptive filters and pattern recognition.
Quality assurance through pattern recognition
Real-time evaluation of measurement data based on pattern recognition: cracks are found and analyzed by means of stored signal patterns. Interfering signals are filtered out. This is followed by immediate transmission of the result (IO/NIO) via Profinet interface.
Plug & Play Retrofit
We retrofit your machine in less than a day. Our retrofit does not require an upgrade of the machine: Same I/Os and same mounting points for the new hardware.
Crack detection with the Optimizer4D
QASS is the world market leader in the field of crack detection during straightening. Especially for straightening machines, we now recommend our new, innovative crack detection system: the Optimizer4D. The Optimizer4D uses a new analysis concept and reduces previously unavoidable pseudo scrap. This occurs when systems incorrectly interpret electrical or mechanical interference signals as cracks.
Conventional crack detection systems analyze the intensity and energy profile of structure-borne noise during straightening. The Optimizer4D adds a third dimension to the analysis: frequency.
With 25,000 spectral analyses per second, Optimizer4D reveals every detail of the straightening process. This makes it possible to distinguish between the signals of a real crack and interference signals. This information can also be used to optimize the process, which reduces scrap even further: crack prevention through improved process recognition.
The microscopic image of a cracked component shows that the crack has closed again after forming on the surface. Many downstream inspection methods such as magnetic particle or laser thermography fail when the surface appears flawless. Optimizer4D detects the crack the moment it appears. This makes it irrelevant whether the damaged area has closed again after the straightening process has been completed.
Top: Crack in a component | Bottom: The crack signal in the process landscape
Would you like to learn more about structure-borne sound?
Our highly accurate measurement method HFIM explained in detail.
Possible applications of crack detection
Here you can find some application examples for our crack detection. If you do not find your process here, please send us an inquiry. We have a lot of experience in the implementation of individual solutions and regularly implement research projects. We are sure to find a solution for your problem as well!
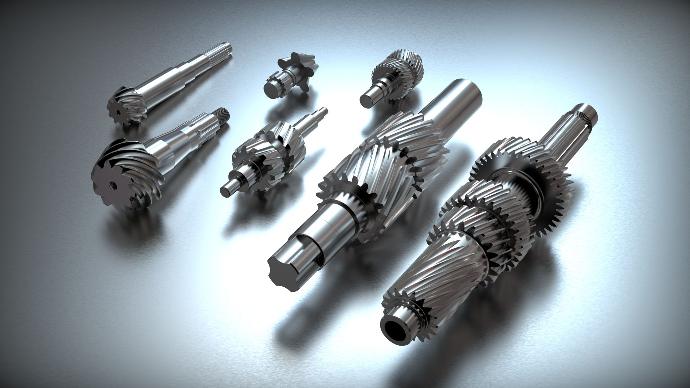
Straightening processes
von Wellen, Stangen, Rohren und Blechen können durch die Umformung des
Materials feinste Haarrisse und andere Rissarten (z.B. Mikrorisse) auftreten. Mittels Körperschalltechnologie gelingt
es QASS, diese in Echtzeit im Serienprozess zu detektieren. So stellen wir sicher, dass Ihre Produktion den höchsten Qualitätsansprüchen
gerecht wird.
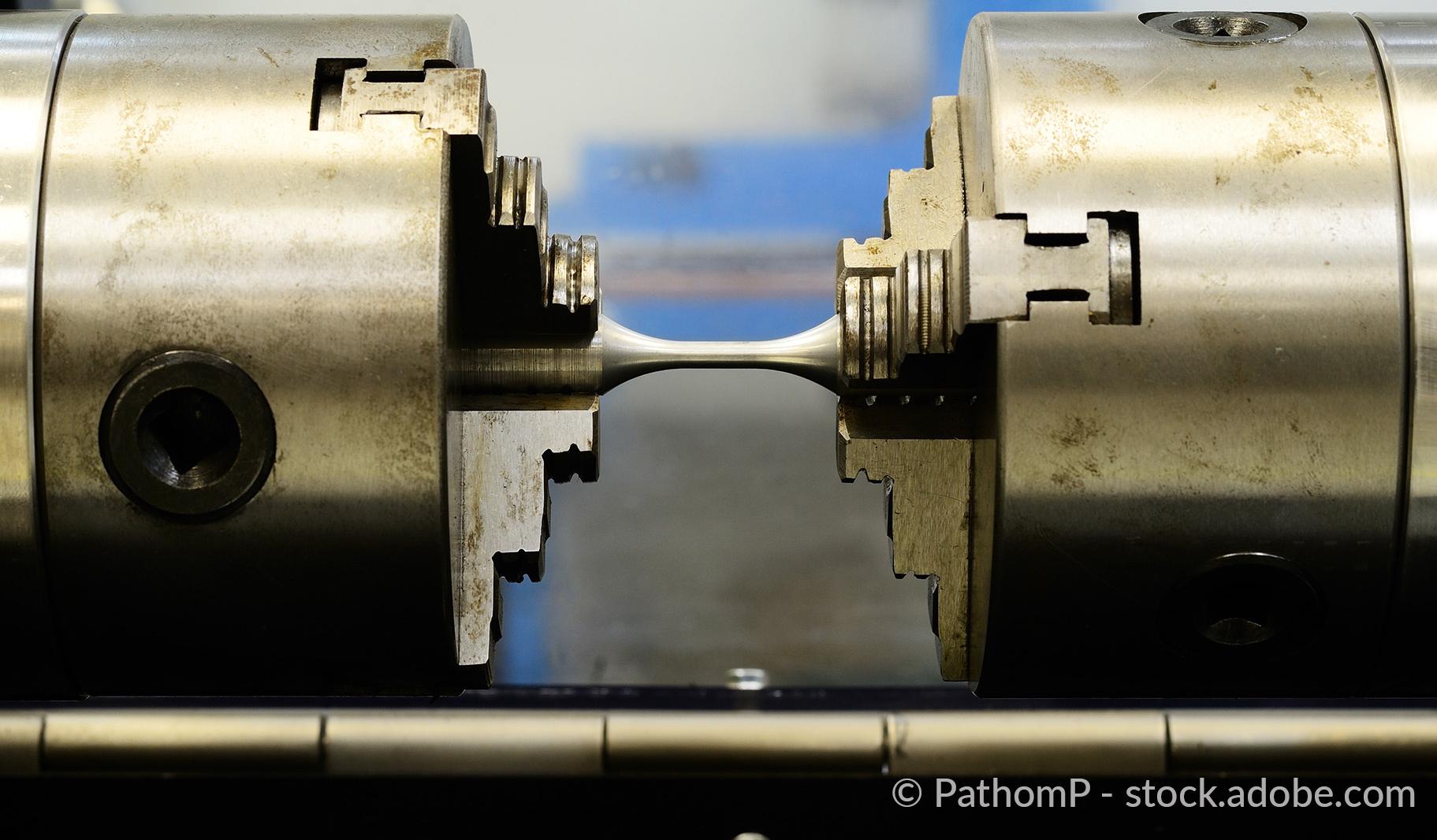
Test stands
Bestimmen Sie die Einsatzgrenzen Ihrer Prozesse durch Körperschallanalyse. Die Rissdetektion von QASS kann bei Umformprozessen, Torsionstestständen und Lagerprüfständen eingesetzt werden. Auch durch White-Etching-Cracks (WEC) entstandene Frühschäden in Lagerprüfständen können mittels Körperschallanalyse detektiert werden.
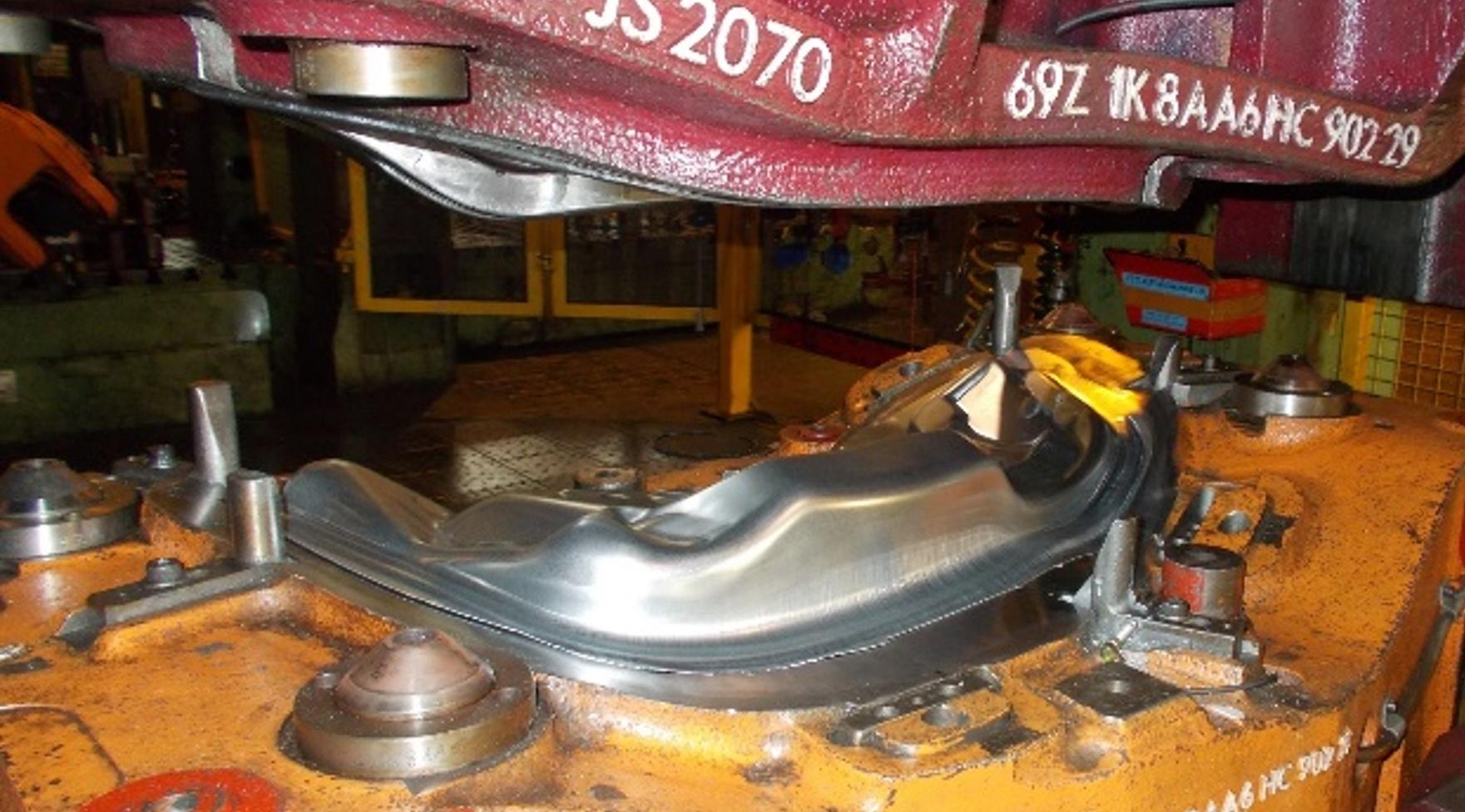
Deep drawing processes
Während des Tiefziehens können schnell Schäden wie Risse auftreten. Mit dem Optimizer4D wird jede Phase des Tiefziehprozesses sichtbar gemacht. Mit der Überwachung und Steuerung des Prozesses können Trends frühzeitig erkannt werden, und ein rechtzeitiges Eingreifen verhindert ein qualitätskritisches Versagen an Bauteilen oder Werkzeugen.
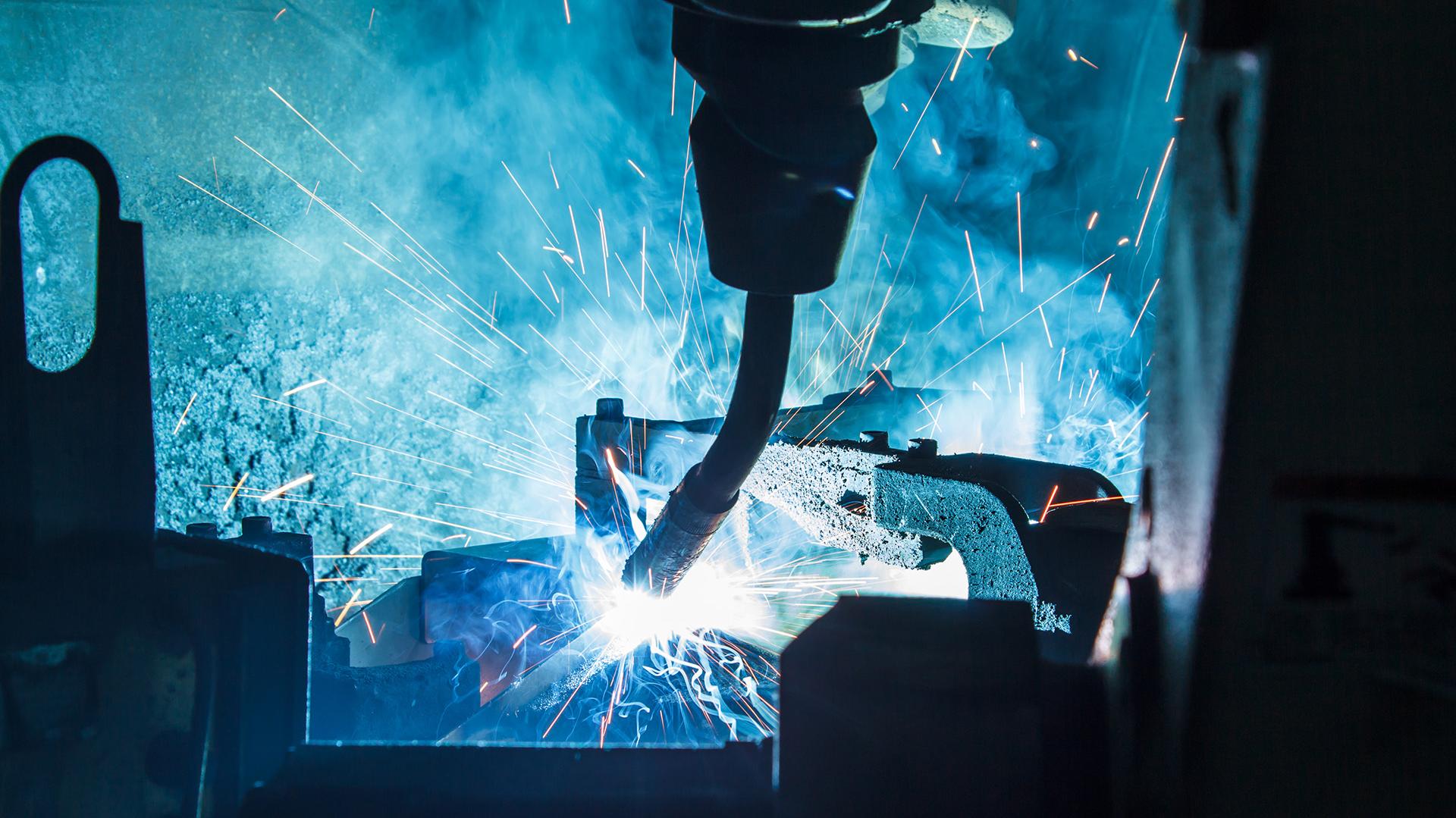
Welding processes
The Optimizer4D not only detects cracks that occur during bending processes but also at all other points where cracks could occur due to plastic deformation or thermal change. The system acts as familiar and proven means of detecting cracks and enables targeted and precise rejection of defective parts despite sometimes enormous ambient noise.
Request
You contact us, by phone or by mail, and describe your situation.
Target definition
We difne the goals of the project together with you
Data analysis
QASS measurement equipment is installed and collects data that is subsequently analyzed.
Application
The measurement technology is specially adapted to your purposes.
Evaluation
Our system is tested and optimized at your site under production conditions.
QASS as a technology partner
QASS has over two decades of experience in process optimization, sensor technology, component monitoring and quality assurance. Our measurement technology, coupled with intelligent pattern recognition software, enables almost 100% crack prevention in straightening processes.
The foundation of our expertise lies in our own research and development efforts, from which new solutions are constantly emerge. Research projects in cooperation with renowned university institutes and well-known companies complement these. We contribute our know-how to the implementation of projects for our customers.
Automotive groups and suppliers worldwide rely on our expertise in crack prevention, process optimization and quality assurance. The continuous development of our products ensures that the monitoring of your straightening process is state-of-the-art. With the help of Optimizer4D, you can therefore not only precisely detect cracks that occur during straightening, but also prevent them from forming in the first place. Through our technology and service, you sustainably reduce the risk of failure of the steel shafts used. In addition, an optimally running straightening process is guaranteed.
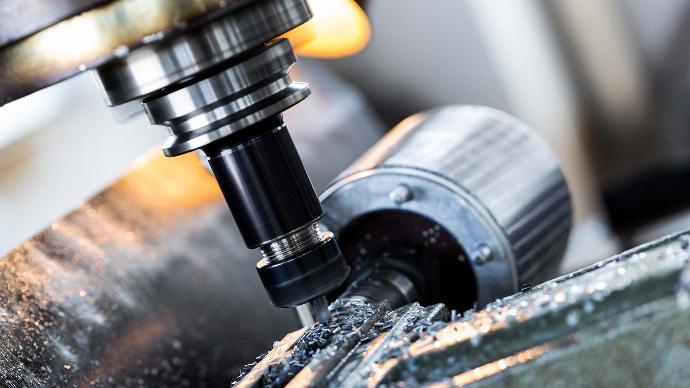
At QASS, we live and love what we do. The basis of our philosophy is the pursuit of ever better results and the search for more efficient ways. See for yourself our solution expertise and our passion for technology and innovation.
Arrange a consultation appointment now!
Ask our experts about the possibilities for your industrial processes without obligation.