Assembly Monitoring
Real-time monitoring of joining and assembly operations
In-line measurement system
Permanent and force-fit connection of the QASS structure-borne sound sensor on the tool (no sensor infeed necessary). Processes can be monitored and evaluated by the Optimizer4D in real time.
Real time data processing
Fast processing of measurement data in real time: 3 million samples per second, spectral processing using Fourier transform, as well as noise reduction with adaptive filters and pattern recognition.
Data analysis through pattern recognition
Engaging noises are detected, evaluated and counted by means of stored signal patterns. Immediate transmission of the result (IO/NIO) after end of measurement via Profinet or OPCUA interface. Integration of all established interfaces is possible.
Attractive system solutions
No cycle time increase thanks to real-time post-process checking of the data. High selectivity through spectral analysis. Cost-efficient overall concept.
What we can detect
- Snap connections
- Engaging procedures
- Cracking of retaining rings
- Press-in operations
- Spring connections
100% in-line quality control
With the Optimizer4D, even hidden and visually inaccessible assembly processes that take place inside components can be reliably checked. The QASS measuring system monitors assembly processes in-line via structure-borne sound and evaluates the process data generated in real time. Defective components or faulty process parameters can thus be detected as soon as they occur.
With our sophisticated data analysis software Analyzer4D, even large amounts of data can be evaluated accurately in real time. In addition to the additional process data gained, the user benefits from a variety of individually configurable and combinable analysis tools and the possibility of combining all parameters.
Sensor fusion - First-class complement for existing measurement technology
The QASS measuring system can be combined with existing systems, such as force-displacement testing, for example. Using TCP/IP, USB or Profinet, further sensors and data streams are processed by the Optimizer4D. With QASS technology, it is already possible today to bring together the data for tomorrow's production.
How it works
The QASS measuring system Optimizer4D works on the basis of structure-borne sound. Each process causes characteristic acoustic impulses, which our measurement system can detect at the moment of occurrence.
The measurement signals are digitally acquired by the Optimizer4D and transformed and processed in real time using Fast Fourier Transform (FFT). This makes them immediately available to the QASS Analyzer4D software. The results are clearly visualized in the QASS 3D spectral landscape.
The use of a frequency mask enables the targeted filtering of typical machine noises. Process events, such as the engagement of the retaining ring, produce specific images in the 3D spectral landscape. These specific signal images can be referenced in the Analyzer4D software and fed into a pattern database so that a comparison algorithm can automatically determine similarities to the stored patterns in further measurements. If the snap-in process does not proceed correctly, this is indicated by the absence of an expected signal image or by deviations in the signal pattern that lie outside the previously defined tolerance limits for the similarity determination.
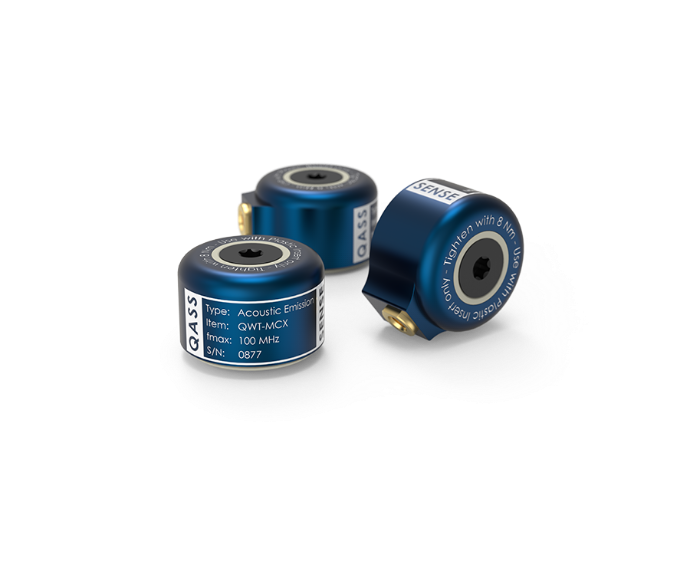
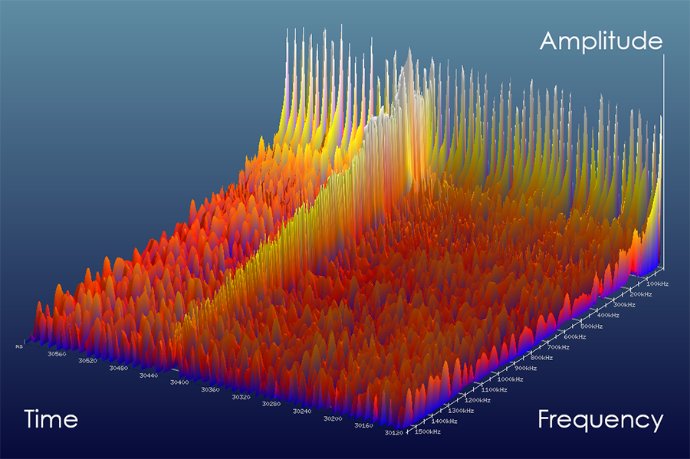
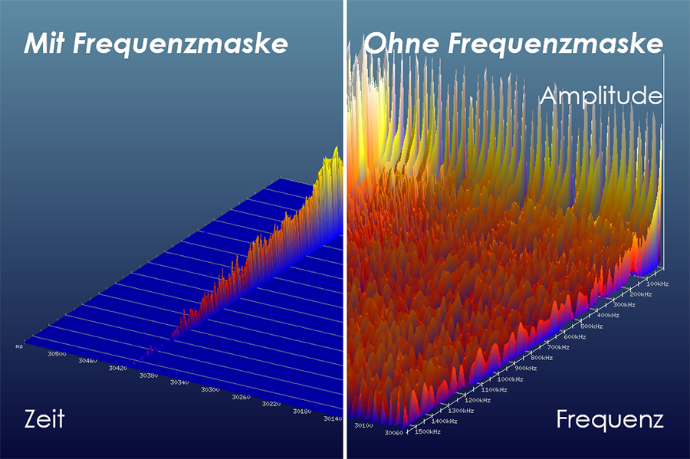
Process examples
The QASS assembly measurement technology in application
Arrange a consultation appointment now!
Ask our experts about the possibilities for your industrial processes without obligation..