Deep drawing
Detect cracks and tool damage early in the process.
Keep an eye on your thermoforming processes
Various damages or issues can occur during deep drawing. With our Optimizer4D measuring system, we can equip your machine with sensors and record and evaluate important signals. Based on the data obtained, we can optimize your deep drawing process according to your needs and detect defects during the formation and reduce waste.
Advantages with QASS
More process reliability
By combining pattern recognition and energy detection, you know what is happening in your process.
Added value for the user
Visualizes the deep drawing process taking place in secret and provides real-time results on component and process quality
Real-time process monitoring
The process is monitored and evaluated in real time. Interference signals are filtered out by adaptive frequency filters.
Fast support
Allows remote access to Optimizer4D and regular software updates.
Application examples
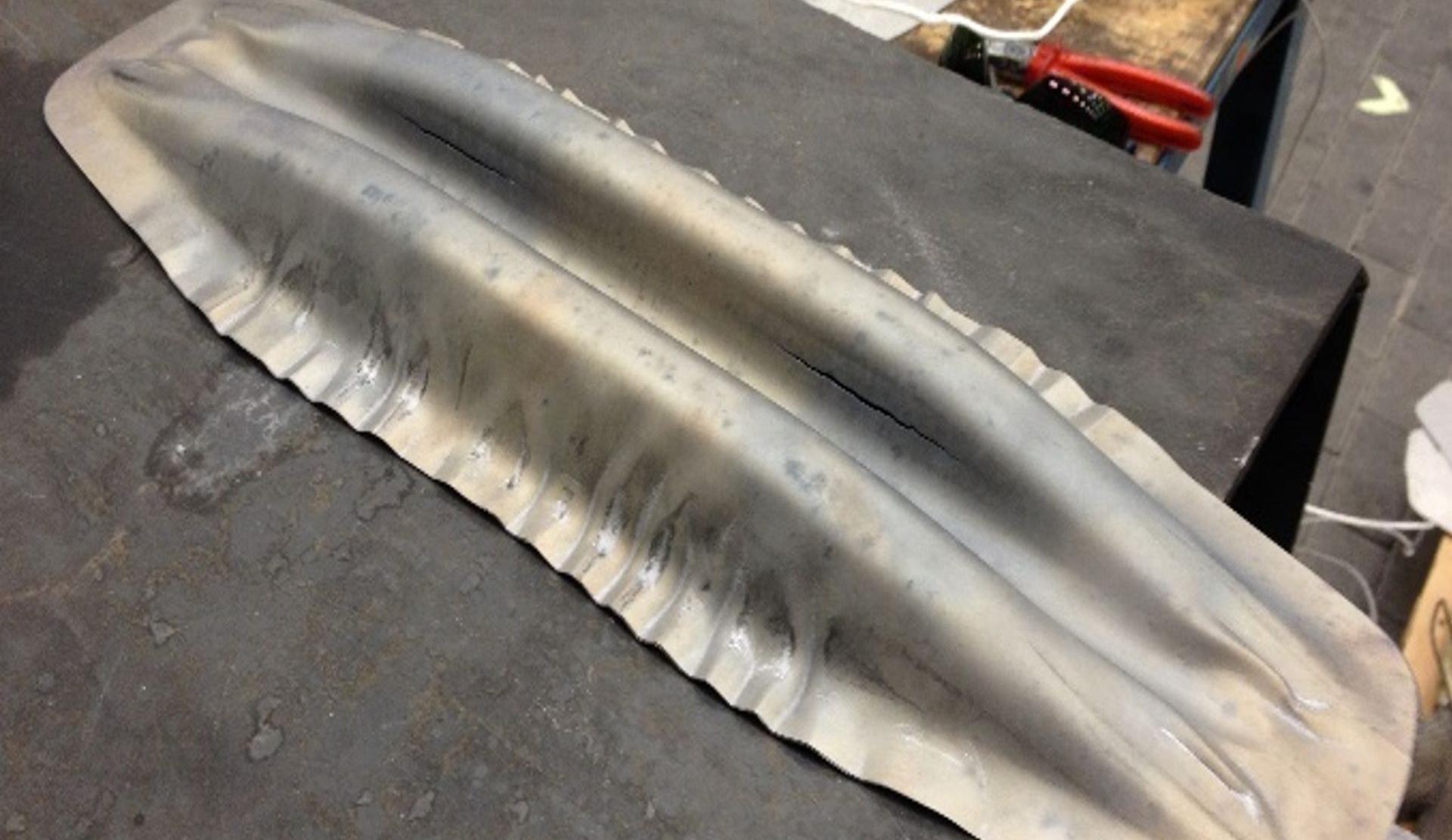
Press hardening
With the help of our vibration sensor, directly mounted on the tool, the various phases of the process can be recorded and visualized in the Analyzer4D software. In this way, undesirable deviations in austenitization or hold-down distance can be detected at an early stage.
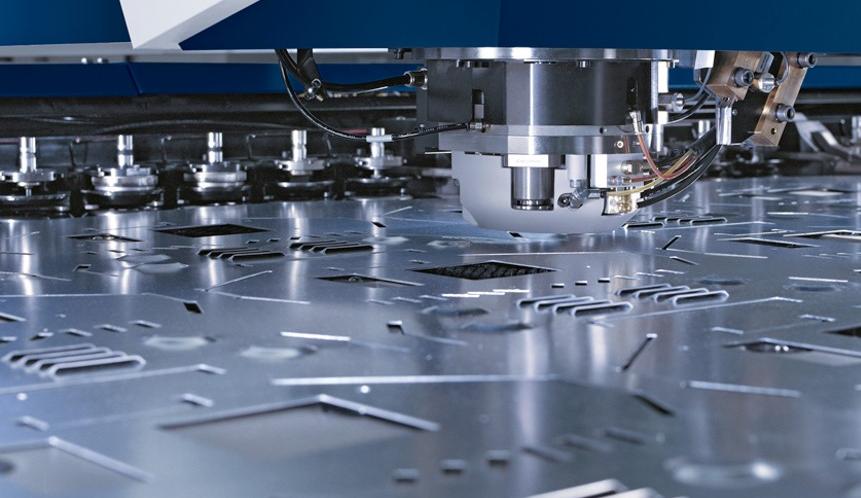
Punching
The Optimizer4D enables the identification of tool wear during shear cutting, such as chipping and filleting. With the QASS measuring system, a longer tool life as well as better cutting quality can be achieved.
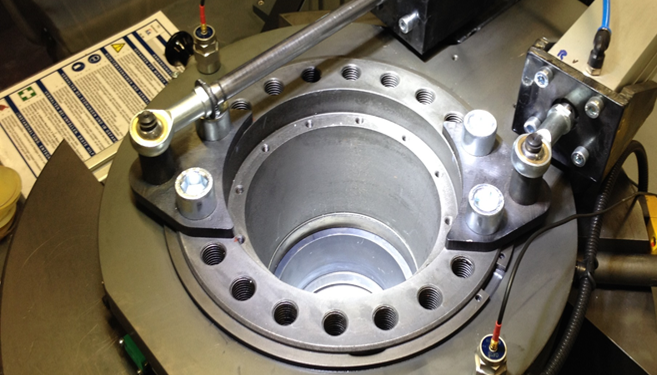
Forming limit
Based on acoustic signals, even the smallest microcracks can be detected with the Optimizer4D. Our measurement technology has been tested using deep-drawing sheets made of various materials.
Deep drawing with the Optimizer4D
Structure-borne sound is a carrier of important process information - even weak signals can be extracted from machine noise using QASS technology. The Optimizer4D enables a robust and industry-ready assessment of the production process through a fast sampling rate, adaptive filtering and innovative pattern recognition. In the long run, downstream inspection is no longer necessary as "listening" is done during the process. Cycle times are not affected. The vibration sensor does not have to be fed, but can be permanently coupled to the machine and enables immediate result transmission via Profinet, Profibus or PLC.
Damage such as cracks or tool damage becomes visible live. Production defects such as thinning, doubling or wrinkles in your thermoforming process can also be detected by our measurement software.
The Optimizer4D measurement system from QASS is suitable for process monitoring, monitoring tribological effects, crack detection and tool monitoring in many different industrial processes.
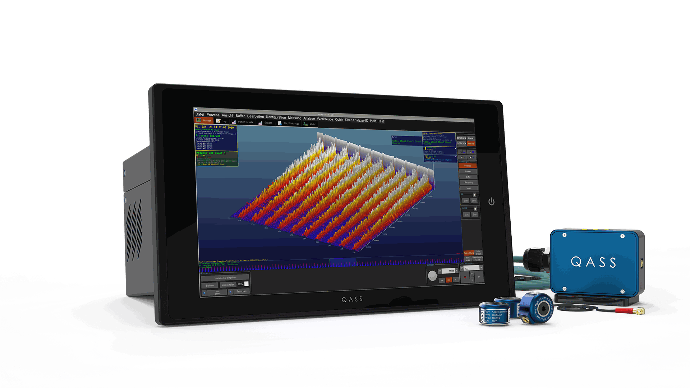
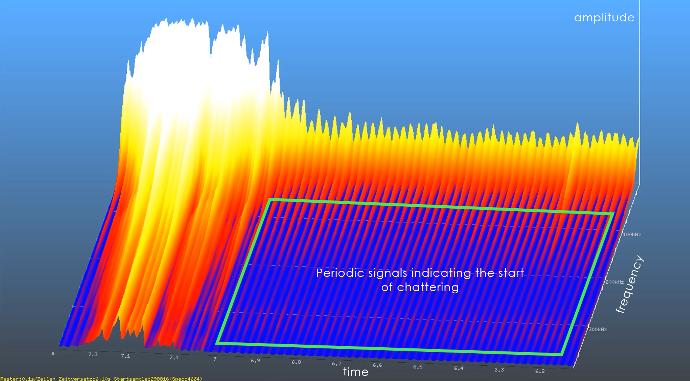
Measurement method structure-borne sound
Using structure-borne sound analysis, essential process signals can be captured in real time. Our measurement system can evaluate these signals and react accordingly to optimize your process.
Arrange a consultation appointment now!
Ask our experts about the possbilities for your industrial processes without obligation.