Prevention of chattering during tube drawing
The QASS measuring system for automated detection of production errors and speed optimization during pipe drawing.
Revolutionize your tube drawing processes with the unique Optimizer4D measuring system from QASS. Make your production more efficient, safer and improve the quality of your products.
Avoid chatter marks
Chatter marks are reliably avoided with our Optimizer4D measuring system in conjunction with our special structure-borne sound sensors. Prevent damage to your products and improve quality.
100 % Inline monitoring
We use our high-performance measuring devices to monitor every single millimeter of the pipe drawing process, at any drawing speed. Manual intervention by the employee is unnecessary.
Increase your drawing speed
Avoiding chatter marks is based on regulating the speed. Have you ever increased the speed when chattering? We show you statistically proven which drawing speed is possible for your pipes.
Retrofit made easy
Our technology can be integrated into any pipe pulling system, regardless of age, manufacturer or condition. We provide customized solutions for machine communication.
QASS measurement technology in use
Chattering is caused by vibrations of the tube in combination with the process parameters, as well as the die and stopper. The vibrations begin imperceptibly until the chattering becomes audible through a clear humming noise.
Our special structure-borne sound sensors detect even the smallest vibrations within the noisy process environment using our patented frequency analysis and electronic filters, despite the large forces and tribological effects of tube drawing. The sensors are installed on the drawing die near the drawing dies. Each drawing die is monitored individually.
Due to various factors acting on each other within the tube drawing process, large oscillations - also called chatter - easily occur. As soon as the chatter starts, unevenness occurs on the material surface. QASS has developed the Optimizer4D for structure-borne noise analysis, the first way to automate testing and optimize the process at the same time.
With the QASS Optimizer4D, vibrations can be detected at an early stage in order to subsequently reduce the drawing speed of the machine. In this way, chatter marks and associated production errors can be avoided.
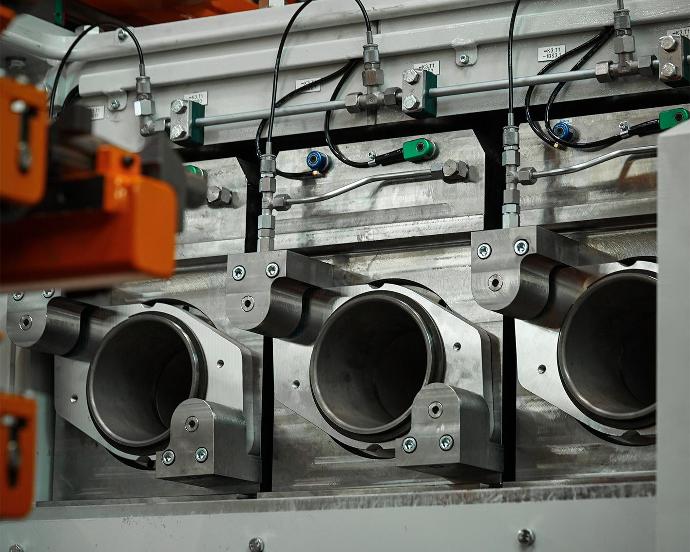
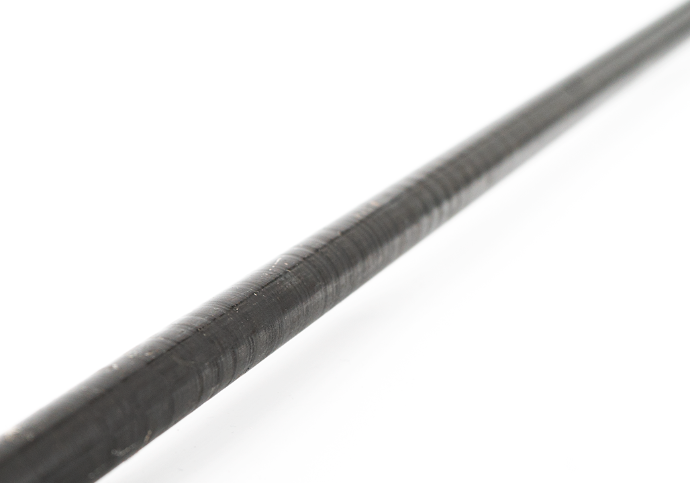
Avoid production errors
We program the data analysis in Python and therefore tailored to your process. With each system, our experience and data basis grows and with it our ability to adapt to the requirements of the pipe run. Our measuring systems are already integrated into many industrial production processes.
We have put a lot of energy into the usability of our product.
usability of our product. The complex interrelationships under the hood should be as easy as possible easy to understand for process experts and machine operators. This has resulted in a operating concept that is constantly being improved.
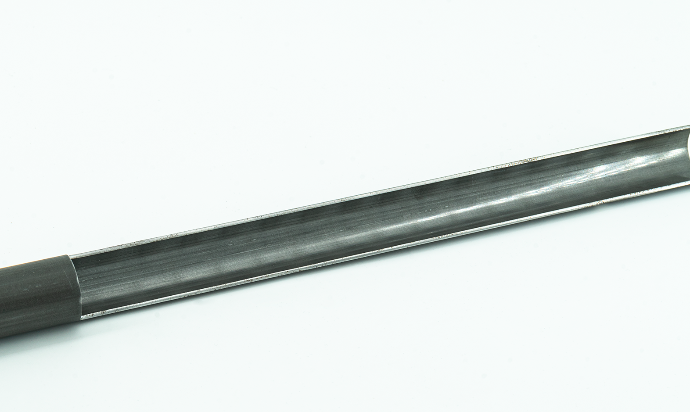
Expertise
Our specialist staff carry out installations, set up the processes on site and closely link the measuring device with the customer's personnel and the control electronics. Our experts are also available to make subsequent improvements to the evaluation. We have also developed strategies and solutions for many different component types and classes to quickly ensure reliable and chatter-free production.
Unbeatable
The decisive variable for suppressing chatter is the drawing speed during pipe drawing. Until now, plant operators have always had one ear for the machine and at least two fingers on the adjustment potentiometer. The QASS Optimizer4D measuring system takes over this task. The drawing speed is briefly reduced by a few meters when a chattering event is detected and then immediately increased again. The chatter event is thus avoided. No benefit?
Then use your drawing machine at a product-specific maximum speed and get the most out of it. Monitoring remains reliable and you will achieve a significant increase in your production on average.
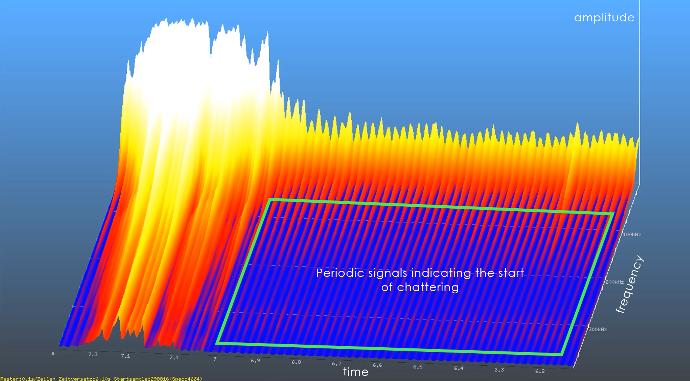
Measurement method structure-borne sound
By means of structure-borne sound analysis, important signals can be detected before damage occurs. The machine speed can be reduced in a timely manner to prevent damage.
Automation of your production process
With the help of structure-borne sound analysis, our process experts have succeeded in detecting the settling of the drawing process before chatter marks occur and in implementing automated control. The measurements are documented and displayed in real time.
QASS' measurement technique uses piezoelectric sensors that detect early vibrations of the tube as a sequence of rapidly occurring micro-pulses before the chatter marks become visible.
Thanks to digital filters for noise suppression, QASS passes even in the most difficult production conditions. Through real-time monitoring and constant connection to the machine's PLC, QASS can automatically reduce the drawing speed for a few seconds. This stabilizes the entire process and averts damage. Subsequently, the speed can be increased again to full load. In this way, QASS reduces the reaction time from minutes to milliseconds.
By converting the analysis concept to programmable content, rapid integration into all types of industrial production environments is possible. The user interface for displaying relevant data is customized by us to meet the needs of our customers.
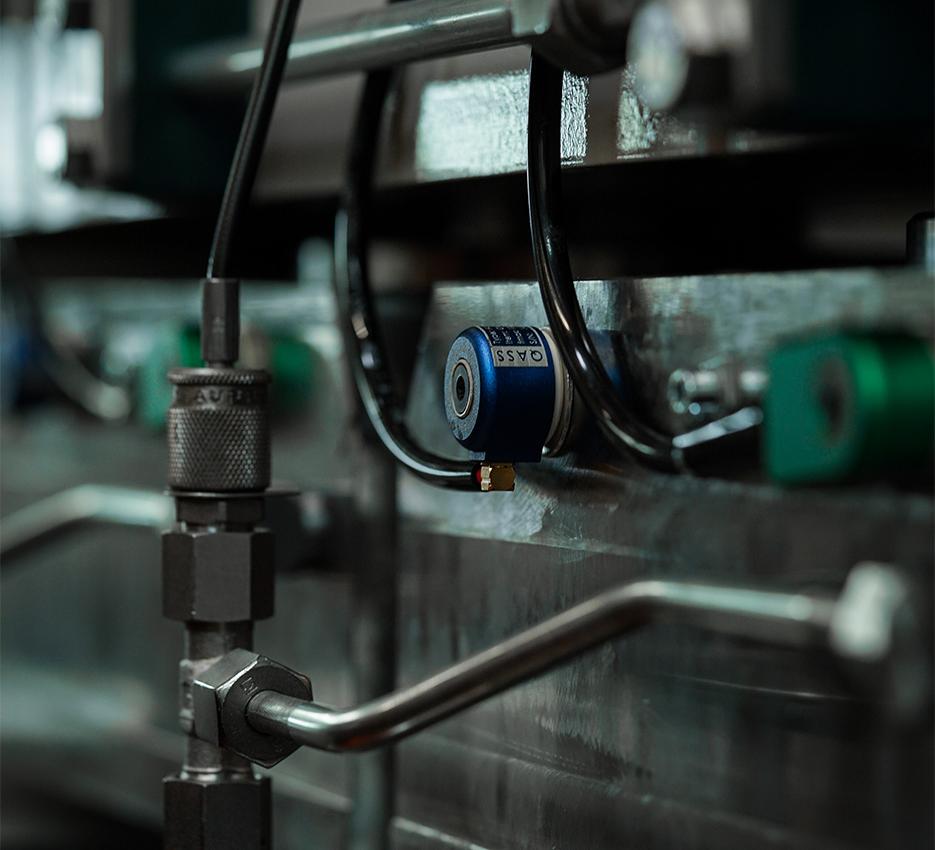
Our Workflow
Request
You contact us, by phone or by mail, and describe your situation
Target definition
We define the goals of the project together with you.
Data analysis
QASS measurement equipment is installed and collects data that is subsequently analyzed.
Application
The measurement technology is specially adapted to your purposes.
Evaluation
Our system is tested and optimized at your site under production conditions.
Arrange a consultation appointment now!
Ask our experts about the possibilities for your industrial processes without obligation.