Bearing test stands
Automated acoustic inspection of bearing test stands
Bearing test stands
Rolling bearings are among the most important machine elements in that they can transmit forces and movements and are used in almost all areas of drive technology. Their designs always depend on the application. In order to ensure smooth and above all long-life operation of rolling bearings, they are lubricated with greases and oils. The lubricants are mixed with additives that give the lubricant additional properties.
However, when additives are used, the properties of the lubricant can be changed in such a way that the operating conditions of the rolling bearing change to unfavorable conditions and the long-life operation of the rolling bearing is jeopardized. For this purpose, the rolling bearings are examined on test rigs and subjected to a test with new oils. For this purpose, acoustic tests and wear tests are carried out.
These DIN standardized tests, e.g. DIN ISO 15242-1 to DIN ISO 15242-3, prescribe a test method to determine the maximum permissible noise development in the bearing. DIN standards, such as DIN 51819, are used to determine the wear using of different lubricants in axial cylindrical roller bearings. Various test rigs are used in these DIN standards.
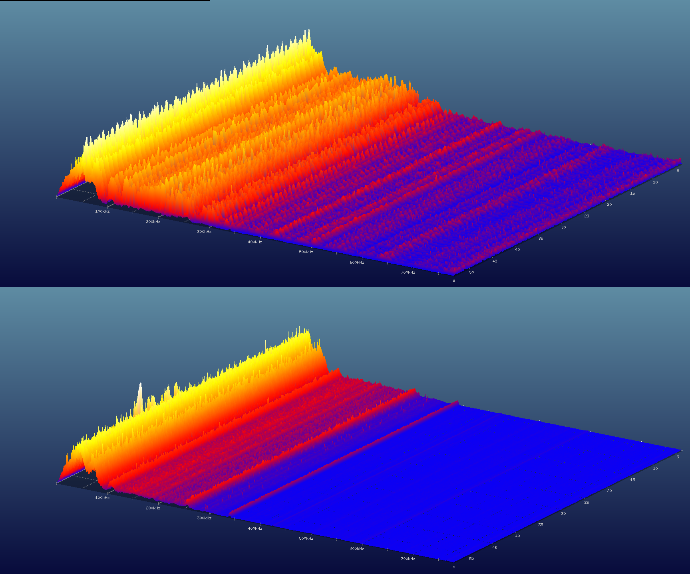
Monitoring with the Optimizer4D
The built-in sensors in the case of the test stands serve to detect the damage to the bearing surface or strong frictional noises during rolling of the rolling elements. The frequencies that are generated are only audible to the human ear to a small extent. Especially the inaudible signals are interesting for the evaluation of the bearing. Certain frequency ranges ≥ 50 kHz describe describe friction noise, uneven bearing operation and the development of early damage. Both microphones and piezoelectric sensors are used. The frequently used acceleration sensors are on the one hand too sluggish and on the other hand not built to detect such high high-frequency signals. Especially since these signals are transmitted in short intervals - a few milliseconds. Acceleration sensors detect the smallest of movements, which can be triggered by pulses, which mainly originate from damage to the rolling bearing surface, but already represent late damage. The damage is done.
QASS Optimizer4D uses vibration sensors to detect the inaudible frequencies. The design of the sensors allows the entire frequency spectrum to pass through, which is then scanned at high frequencies of up to 100 MHz. The simultaneous high data acquisition rate means that no change in the bearing system goes undetected. The vibration sensors convert the inaudible noise into electrical current, which is available with good temporal resolution as a time-amplitude signal. The signal is directly subjected to a mathematical transformation (Fast Fourier Transform), resulting in additional information. The signal is represented in such a way that an assignment of the corresponding frequency components with respect to their amplitude at a certain point in time is created. The resulting spectra provide a comprehensive overview of the qualitative condition of the rolling bearing and lubricant.
This technology can detect friction noise and the smallest unevenness of the
surface of rolling bearings can be detected. The friction noises are dependent on the type of lubricant used and, to a large extent, on the additives dependent on the additives used. Figure 1 shows a comparison between two lubricants of an FE-8 test, which are based on a common base lubricant. The lubricants differ only in the combination of their
additives. The ratio of the wear protection additives is different in this case. The test was carried out at the same axial pressure and temperature in an FE-8 test rig.
Arrange a consultation appointment now!
Ask our experts about the possibilities for your industrial processes without obligation.