Zelos-Anlage zur Homogenitätsprüfung
Unsere Systemlösung zur Prüfung von pulvermetallurgischen Bauteilen und Grünlingen.
Zelos-Anlage zur
Homogenitätsprüfung
von pulvermetallurgischen Bauteilen und Grünlingen
Die Zelos-Anlage wurde von QASS mit dem Ziel entwickelt, Unternehmen in der Qualitätssicherung beim Sintern zu unterstützen. Zelos ist eine automatisierte Laboranlage zur Überprüfung der Verdichtung bei gesinterten Bauteilen.
Das in der Anlage verbaute Messsystem ist der QASS Optimizer4D mit µmagnetic– der mikromagnetischen Erweiterung zur Härteprüfung, Schleifbrandprüfung und Segmentdichte-Prüfung für Sinterteile und Grünlinge.
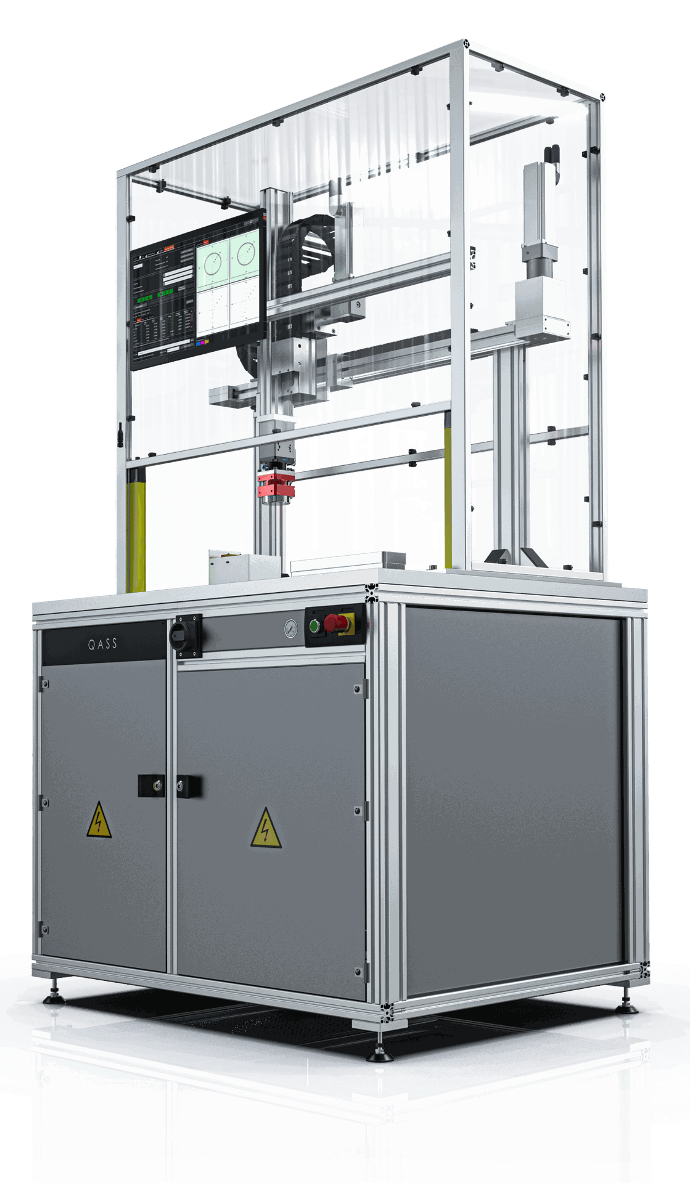
Zelos-Merkmale
Features im Überblick
Einfache Nutzung und Übersicht
Adaptive und speziell auf die Anlage abgepasste Benutzeroberfläche
vereint Konfiguration, Steuerung und Ergebnisdarstellung für den Nutzer.
Flexible Anpassung
Nicht nur die Anzahl der zu testenden Prüfkörper, sondern auch die Anzahl der Messpositionen sowie die Anzahl der Messwiederholungen pro Position und Toleranzgrenzen sind frei einstellbar.
In Serie integrierbar
Die Zelos-Anlage ist einfach in der bestehenden Serienproduktion integrierbar.
Ablauf der Homogenitätsprüfung
Homogenitätsprüfung von Grünlingen mit dem Optimizer4D
Schonendes Bauteil-Handling
Prüflinge werden mittels eines pneumatisch gesteuerten Magnetgreifers sanft aus der Halterung entnommen und über zwei Linearachsen zum mikromagnetischen Sensor geführt.
Mikromagnetische Vermessung
Unsere Sensoren zeichnen die Barkhausen-Signale auf, die als Reaktion auf die Magnetisierung durch ein externes magnetisches Wechselfeld entstehen.
Analyse mit dem Optimizer4D
Die Barkhausen-Signale werden im
Optimizer4D
von der Analyzer4D-Software verarbeitet und mittels Spektralanalyse, Mustererkennung und Energiedetektion ausgewertet.
Jetzt Beratungstermin vereinbaren!
Informieren Sie sich unverbindlich bei unseren Experten über die Möglichkeiten für Ihre Industrieprozesse.