Risserkennung bei der Herstellung von Federn
Risse zuverlässig und automatisiert erkennen mit dem QASS-Messsystem.
Inline-Risserkennung
QASS ermöglicht eine Echtzeit-Risserkennung beim Winden von Federn. Wir überwachen jede Millisekunde des Prozesses und fehlerhafte Bauteile werden automatisch vom System ausgeschleust.
Datenanalyse durch Mustererkennung
Echtzeit-Auswertung der Messdaten anhand Mustererkennung: Risse werden mittels hinterlegter Signalmuster gefunden und analysiert. Es folgt die unmittelbare Übermittlung des Ergebnisses (IO/NIO) durch gängige SPS-Schnittstelle.
Volle Qualitätskontrolle
Windeprozesse werden von unseren Körperschallsensoren lückenlos überwacht und minimieren den Bedarf an nachgelagerten Qualitätsprüfungen. Das System arbeitet voll-automatisch und Sichtproben werden überflüssig.
100% zerstörungsfreie Überwachung
Auf Grund unseres auf Körperschall basierten Messprinzips zeichnen unsere Sensoren alle Details Ihres Prozesses völlig zerstörungsfrei auf.
Risserkennung in der Federnfertigung
Lückenlose Überwachung während der Federnherstellung für höchste Qualität und Sicherheit
In der Federnherstellung wird branchenübergreifend das Ziel
verfolgt, die Sicherheitsstandards zu erhöhen und Problemen wie Rissen und
Defekten entgegenzuwirken. Eine effiziente Qualitätssicherung bei der
Herstellung ist von entscheidender Bedeutung, um diese Schäden frühzeitig zu
erkennen und Austauschvorgänge zu vermeiden.
Während der Produktion durchlaufen Federn mehrere Schritte, darunter
Kaltumformung, Anlassen und Setzen. Im Rahmen der Kaltumformung werden Federn
hohen Druck- und Zugkräften ausgesetzt, was maßgeblichen Einfluss auf ihre
mechanischen Eigenschaften, insbesondere auf ihre Festigkeit und Flexibilität,
nimmt. Trotz fortschrittlicher Technologien bleibt oft die visuelle Kontrolle
durch Menschen als letzte Sicherheitsmaßnahme notwendig, da Techniken wie
Magna-Flux bei der Vielzahl an Federn ineffektiv sein können.
Zur Qualitätssicherung hat QASS ein Komplettsystem entwickelt, das eine automatische und Echtzeit-Detektion von Rissen ermöglicht. Mithilfe von Mustererkennung werden Rissmuster im gesamten Schwingungsmuster identifiziert. Das Messgerät Optimizer4D spielt hierbei eine zentrale Rolle, da es diese Analyse-Methodik für die Serienproduktion inklusive Maschinenkommunikation bereitstellt. Die Einführung von Körperschallsensorik, wie sie in der Automobilindustrie bereits Standard ist, ermöglicht eine präzise Risserkennung und gewährleistet eine 100% rissgeprüfte Auslieferung.
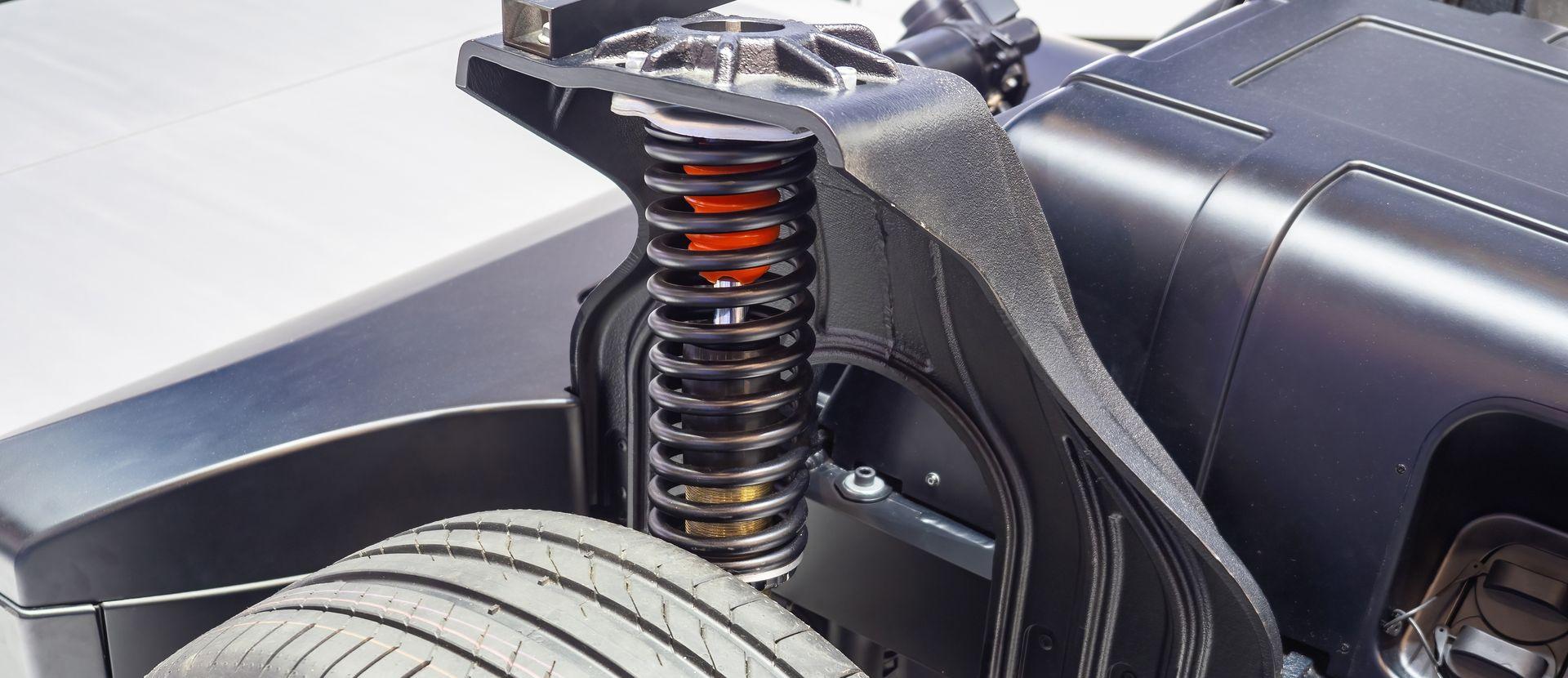
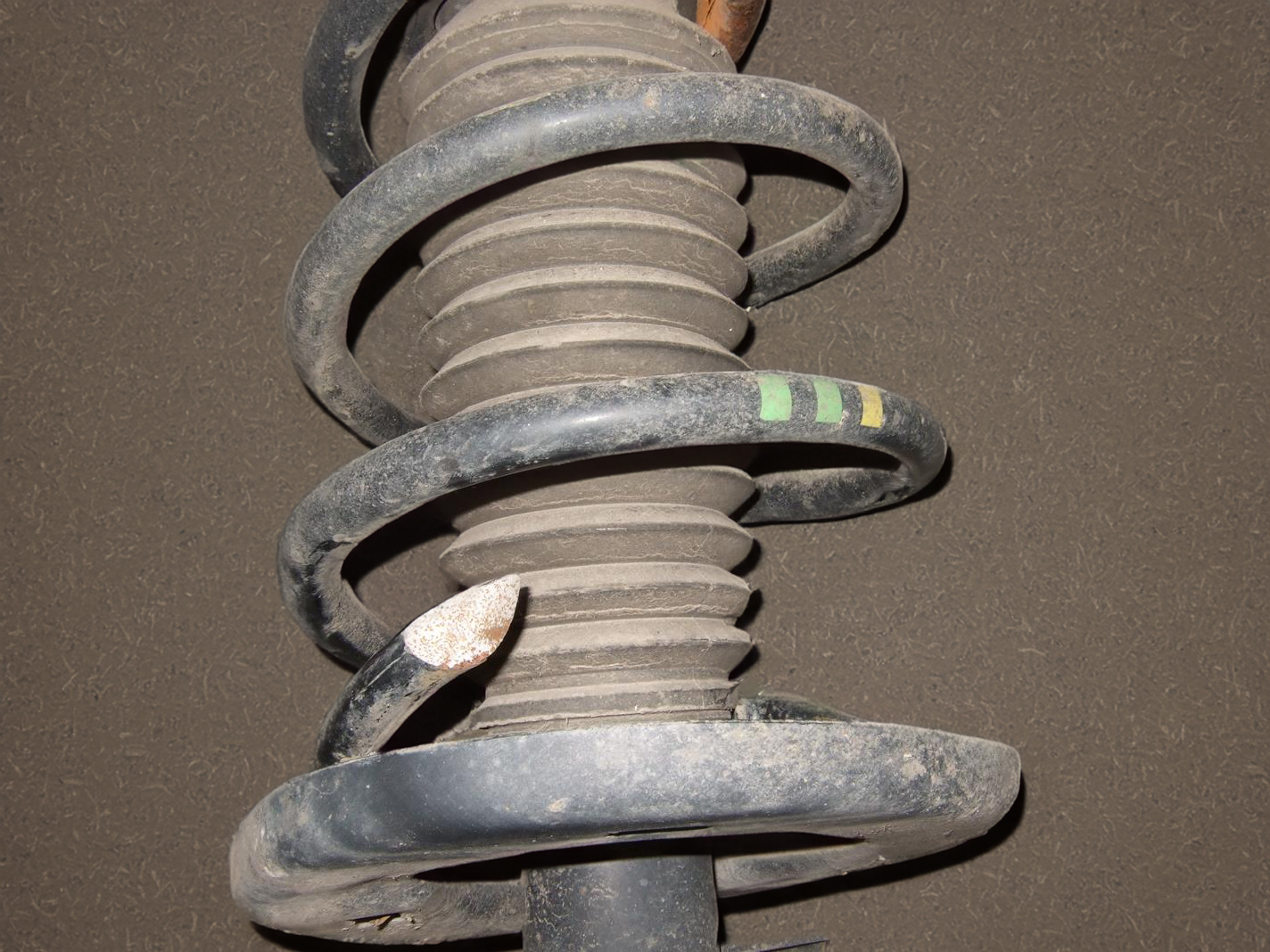
Abbildung 2: Nahaufnahme einer gerissenen Fahrzeugfeder
Ihre Branchen
Automotiv
Luft- und Raumfahrt
Windenergie
Medizintechnik
Maschinenbau
So funktioniert es
Der QASS Optimizer4D im Einsatz
QASS-Sensor installieren
Die Installation der Körperschallsensoren erfolgt an der Winde– oder Setzmaschine. Beim Winden von Draht entstehen Reibung und Umformkräfte innerhalb der Maschine, die Geräusche erzeugt.
Diese Geräusche sind zwar für das menschliche Ohr ab einer Frequenz von über 20 kHz nicht wahrnehmbar, werden jedoch innerhalb der Maschine übertragen und können von QASS-Sensoren erfasst werden.
Bereits kleinste Unterschiede von der Norm erzeugen Abweichungen im gesamten Emissionsbild während des Umformprozesses. Wichtig ist eine einfache Verschraubung an die Maschine, sodass die Schwingungen und Emissionen des Prozesses durch das Material an die Sensoren übertragen werden.
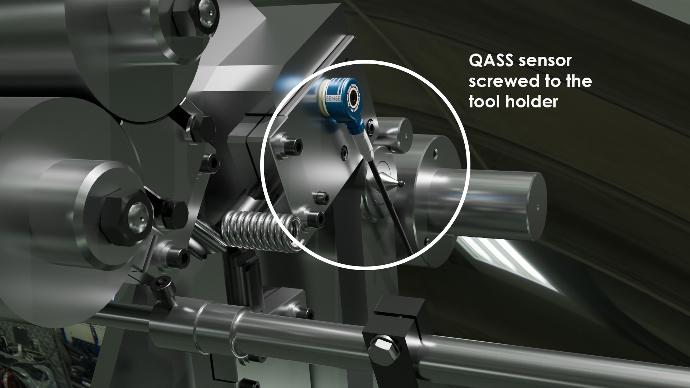
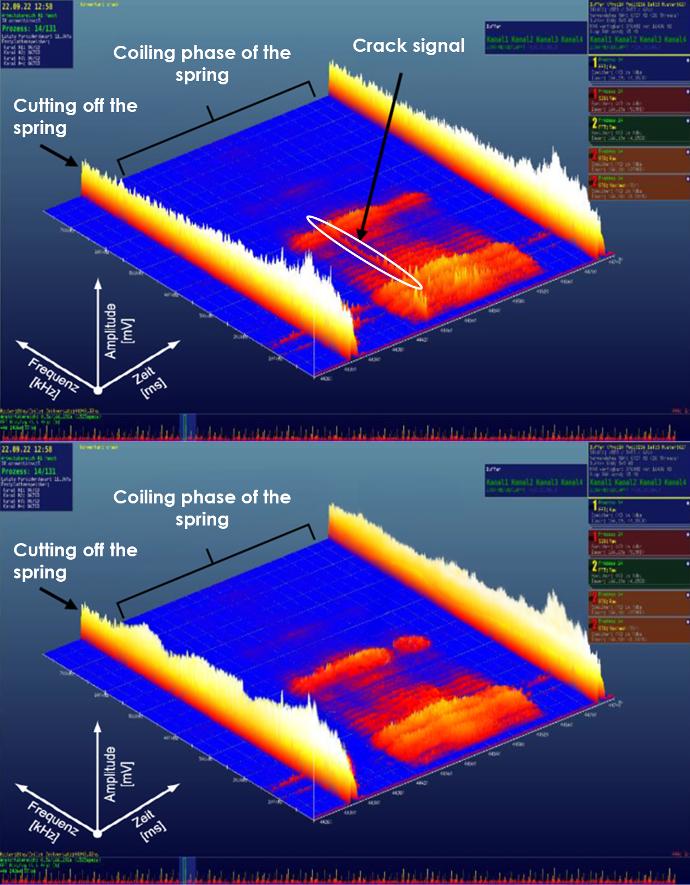
Immer wenn ein Riss in festem Material durch Umformkräfte
entsteht, laufen Druckwellen durch das Bauteil. Die Intensität dieser Welle ist
umso stärker, je fester das Gefüge ist.
Es gilt, diese
Emissionen von den normalen Maschinengeräuschen zu unterscheiden.
Hierzu wird der "Optimizer4D" eingesetzt, unser leistungsstarkes Messsystem, dass Körperschalldaten in Echtzeit erfassen und auswerten kann. So ist es möglich, dass Auftreten von Rissen zu bemerken und das beschädigte Bauteil auszusortieren.
Die QASS-Spektralanalyse ermöglicht es, alle Arbeits- und Störgeräusche der Maschine zu trennen, sodass selbst Mikrorisse bei ihrer Entstehung zuverlässig detektiert werden können.
Die aufgenommenen Körperschallsignale lassen sich, wie im Bild (links) dargestellt, in unserer FFT-Landschaft anzeigen und nachvollziehen. Unsere essentiellen Features wie Clustering und die damit verbundene Mustererkennung, sowie entsprechende Frequenzfilter und -masken, ermöglichen es uns, wichtige Signale von Stör- oder Maschinengeräuschen präzise zu trennen und diese innerhalb von Millisekunden analysieren.
Der Optimizer4D kann nicht nur zur Detektion von Rissen genutzt werden. Körperschalldaten sind Fingerabdrücke von Fertigungsprozessen und Maschinen. Nutzen Elemente der Werkzeuge, wie bspw. Windestifte oder Führungsrollen, ab, so ist dies in den Körperschalldaten zu erkennen. Mangelhaftes Vormaterial gibt andere Signale ab, als solches, das von guter Qualität ist. QASS verschafft seinen Kunden tiefere Einblicke in ihre Prozesse, zeigt frühzeitig an, wenn Maschinen eine Wartung benötigen und liefert seinen Kunden wichtige Informationen über das gelieferte Vormaterial des Drahtherstellers.
Anwender von QASS-Messsensorik profitieren von
- Zuverlässige Riss- und Mikrorissdetektion
Risse, die kritische Größe erreichen, können vom Optimizer4D erkannt und ausgeschleust werden. Eine Warnung wird automatisch an das System weitergegeben.
- Überwachung des Werkzeugzustands (Tool
Monitoring)
Unser Messsystem ermöglicht nicht nur die Detektion von Rissen, sondern kann Beschädigungen am Werkzeug der Maschinen feststellen (z.B. Abnutzung der Windestifte) - Qualitätsbeurteilung des Vormaterials
Anhand charakteristischer Unterschiede der Körperschalldaten, können wir auf Risse im Vormaterial schließen.
Risse erkennen, Vormaterial bewerten, Verschleiß am Windewerkzeug detektieren,
Maschinentrends verfolgen – der Optimizer4D macht all dies möglich.
Unser Konzept
Die Überwachung des Federwindeprozesses gliedert sich in drei Grade der Komplexität:
Basic
In der Basic-Fassung des Überwachungsmodells ist eine
Prozessüberwachung aktiviert. Diese dient dazu, die Entwicklung von
Körperschallsignalen im Prozess selbst zu überwachen. Unser Messsystem,
Optimizer4D, ermöglicht nicht nur die Detektion von Mikrorissen, sondern auch
die Bewertung der Materialqualität vor dem Winden. Zudem lassen sich
Beschädigungen an Windestiften feststellen. Die Kontrolle der Zuführwalzen ist
je nach Anzahl und Position der montierten Sensoren ebenfalls möglich.
Advanced
Zusätzlich zu den Vorzügen, die aus der
Basic-Überwachung resultieren, ist die „Advanced“-Version mit einer Risserkennung
ausgestattet. Risse, die kritische Größe erreichen, können vom Optimizer4D
erkannt und ausgeschleust werden. Eine Warnung wird automatisch an das System
weitergegeben.
Expert
Über die Benefits von „Basic“ und „Advanced“ hinaus
bietet das Expertenlevel die Möglichkeit, den Prozess noch weiter zu
analysieren. Es ist nun möglich, Mikrorisse zu detektieren, weitere
Sensorquellen anzuschließen, um mehr Daten auswerten zu können und mittels
KI/Machine Learning Metaaussagen über den Prozess zu treffen. Dieses Level ist ideal für erfahrene Anwender, die nicht nur ihre
Prozesse wirtschaftlich und technisch optimieren möchten, sondern auch ein
tiefes Verständnis für die zugrunde liegenden Mechaniken und Korrelationen
anstreben, um den gesamten Prozess zu verbessern und besser zu durchschauen.
Lieferumfang
Optimizer4D Messcomputer
2TB SSD Festplatte
Optimizer4D Messkette (Vorverstärker, Körperschallsensor, Kabel)
12“ o. 15“ Touch Display
Der Optimizer4D ist vorgesehen für den Einbau in einen Maschinenschaltschrank.
Dieser muss klimatisiert sein, bzw. über eine Lüftung verfügen.
Optionen
8TB Festplatte anstatt der 2TB
Unterbringung des Optimizers in einem eigenen Schaltschrank (gegen
Aufpreis)
Unterbringung des Optimizers in einem mobilen „Expertenkoffer“ (gegen Aufpreis)
Maschinenkommunikation
24V/IO-Kommunikation ( inklusive )
ProfiBus ( gegen Aufpreis )
ProfiNet ( gegen Aufpreis )
Graphical User Interface ( GUI )
Das Userinterface des Optimizers verfügt über mehrere Ebenen. Die oberste
und für alle sichtbare Ebene ist die „PenGUI“ ein anpassbares Interface, auf
dem die einfachsten Informationen leicht und intuitiv einsehbar sind.
Rissquoten, Trendentwicklungen, oder einfache „Rot“-„Grün“ Anzeigen geben dem
Maschinenbediener schnell und verständlich die nötigen Informationen.
Loggt sich jemand mit höherem Zugriffsrecht ein, kann dieser tiefer in den
Prozess eintauchen, sich Signale im Rohzustand anzeigen lassen, die
Musterbibliothek anpassen, etc.
Das Augenmerk liegt darauf, an der Maschine nur die absolut notwendigen Daten
anzuzeigen.
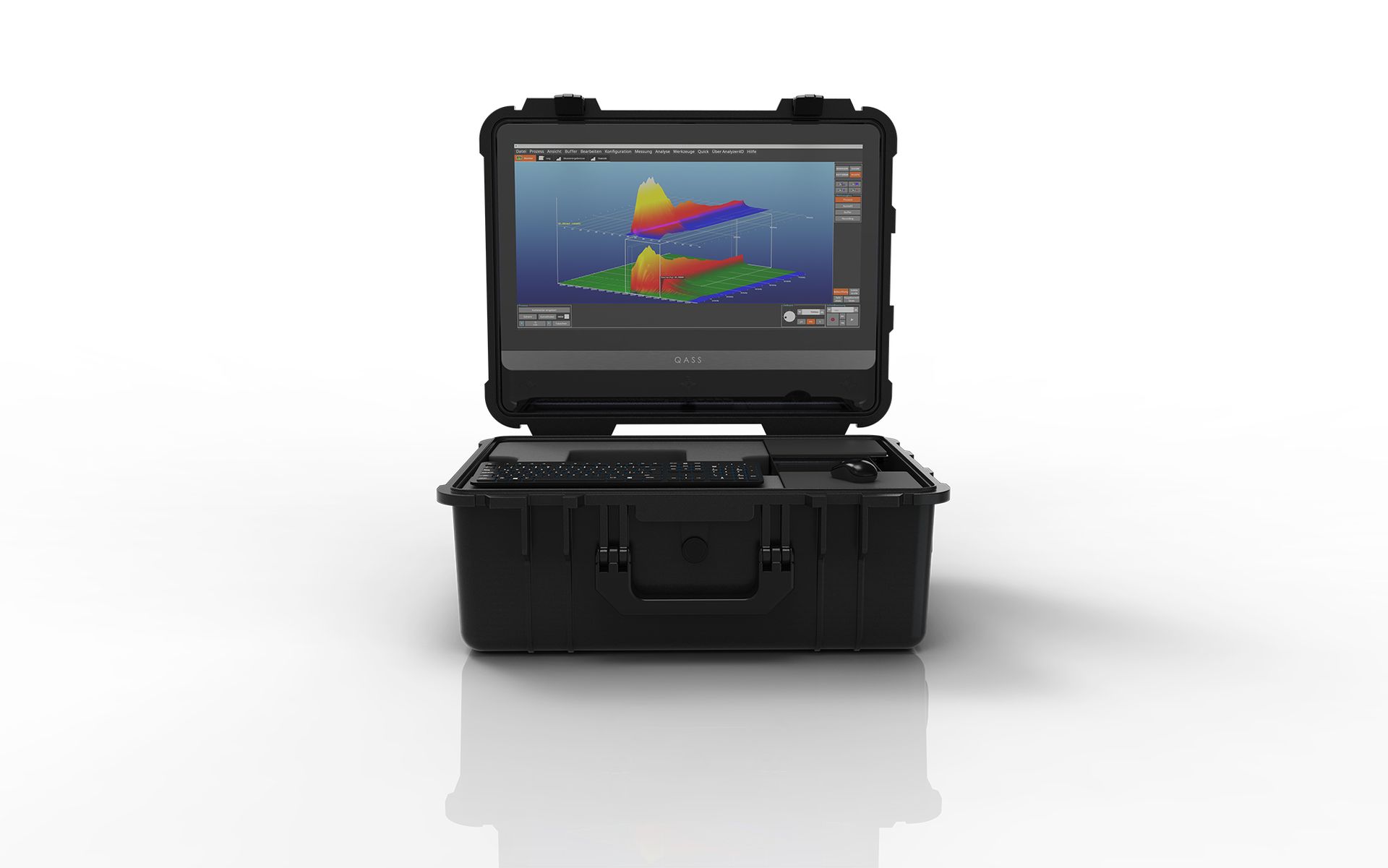
Anfrage
Sie nehmen mit uns, telefonisch oder per Mail, Kontakt auf und schildern uns Ihre Situation
Zieldefinition
Wir definieren gemeinsam mit Ihnen die Ziele des Projekts.
Datenanalyse
Die QASS Messtechnik wird installiert und erfasst Daten, die im Anschluss analysiert werden.
Applikation
Die Messtechnik wird speziell auf Ihre Zwecke angepasst.
Evaluation
Unser System wird bei Ihnen unter Produktionsbedingungen getestet und optimiert.
Jetzt Beratungstermin vereinbaren!
Informieren Sie sich unverbindlich bei unseren Experten über die Möglichkeiten für Ihre Industrieprozesse.