Tiefziehen
Frühzeitig Risse und Werkzeugschäden im Prozess erkennen.
Behalten Sie Ihre Tiefziehprozesse im Blick
Während des Tiefziehens können verschiedene Schäden oder Probleme auftreten. Mit unserem Optimizer4D-Messsystem können wir Ihre Maschine mit Sensoren ausstatten und wichtige Signale erfassen und auswerten. Anhand der gewonnen Daten können wir Ihren Tiefziehprozess bedarfsgerecht optimieren und Fehler während der Entstehung erkennen sowie den Ausschuss senken.
Vorteile mit QASS
Mehr Prozesssicherheit
Durch die Kombination von Mustererkennung und Energiedetektion wissen Sie, was in Ihrem Prozess passiert.
Mehrwert für den Anwender
Visualisiert den im Verborgenen stattfindenden Tiefziehprozess und liefert Echtzeit-Ergebnisse zur Bauteil- und Prozessqualität.
Prozessüberwachung in Echtzeit
Der Prozess wird in Echtzeit überwacht und ausgewertet. Störsignale werden durch adaptive Frequenzfilter herausgefiltert.
Schneller Service
Ermöglicht Remote-Zugriff auf Optimizer4D und regelmäßige Software-Updates.
Anwendungsbeispiele
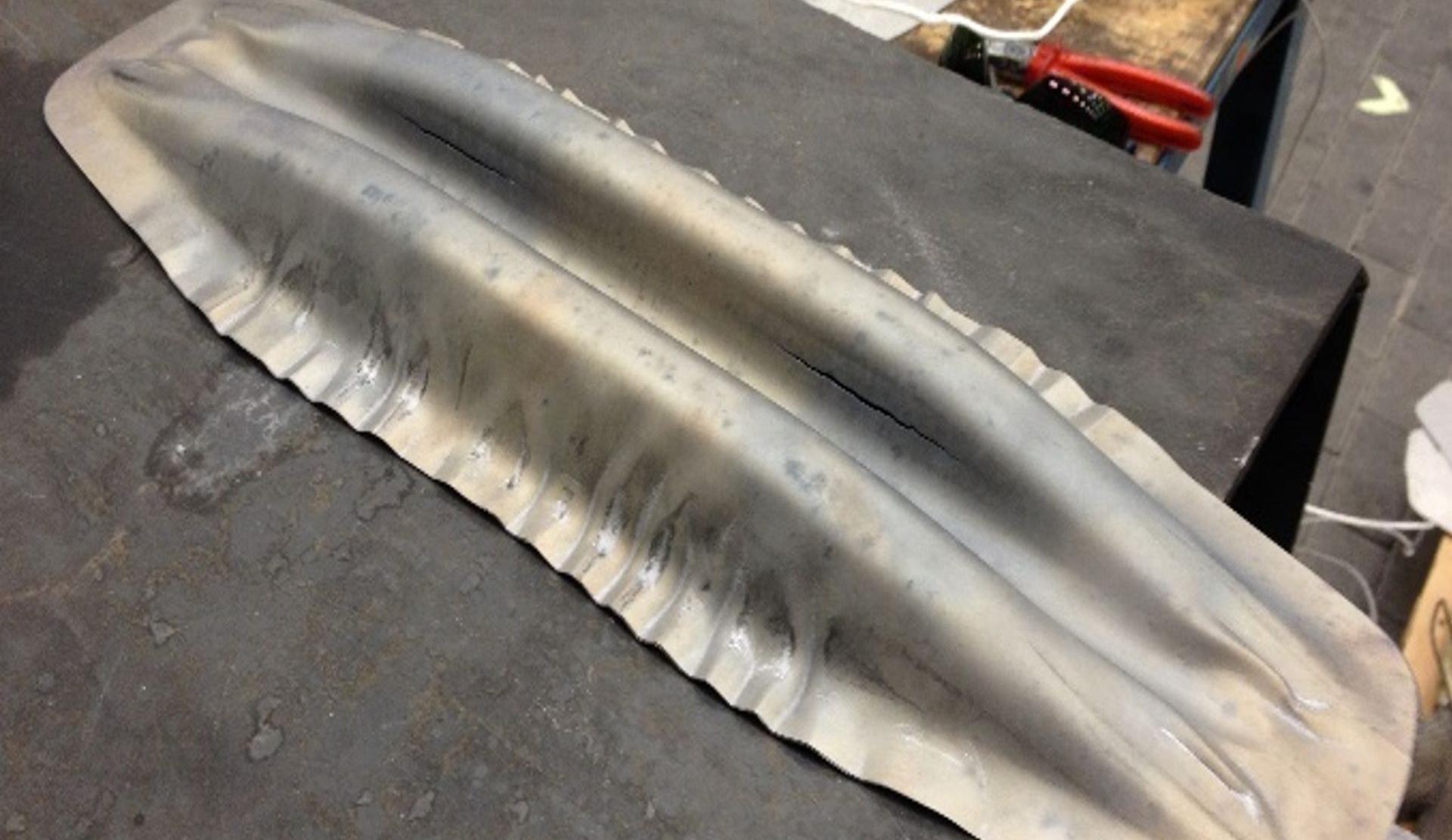
Presshärten
Mithilfe unseres Vibrationssensors, der direkt am Werkzeug angebracht ist, können die verschiedenen Phasen des Prozesses erfasst und in der Analyzer4D-Software visualisiert werden. Auf diese Weise lassen sich frühzeitig unerwünschte Abweichungen in der Austenitisierung oder der Niederhalterdistanzierung erkennen.
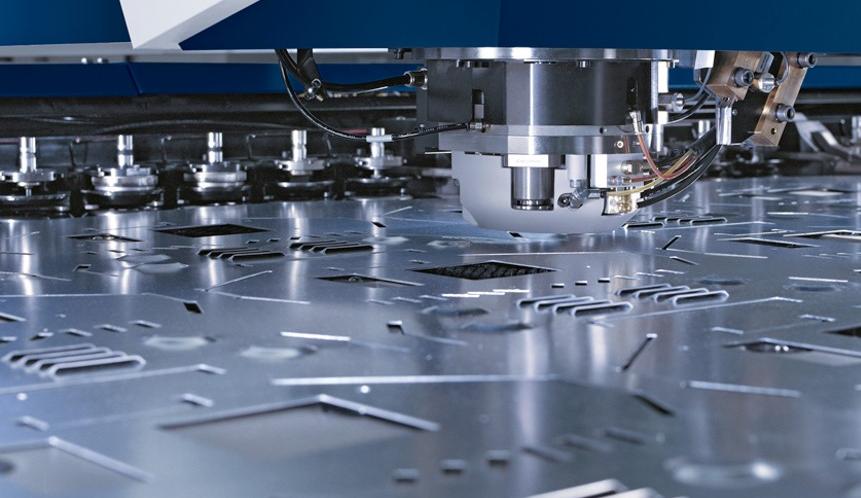
Stanzen
Der Optimizer4D ermöglicht die Identifikation von Werkzeugverschleiß beim Scherschneiden, wie z. B. Ausbrüche und Verrundungen. Mit dem QASS-Messsystem kann eine längere Werkzeugstandzeit sowie eine bessere Schneidqualität erzielt werden.
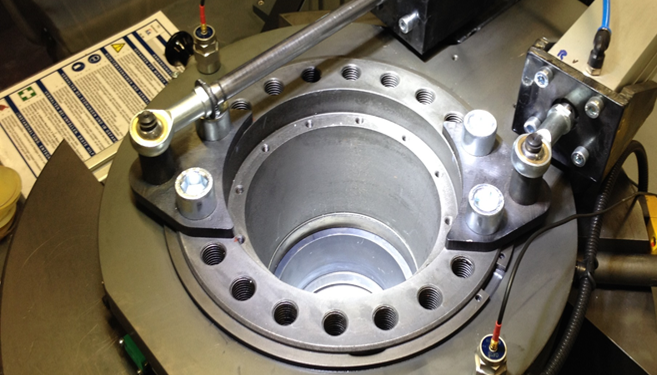
Grenzformänderung
Anhand von akustischen Signalen können selbst kleinste Mikrorisse mit dem Optimizer4D erkannt werden. Unsere Messtechnik wurde anhand von Tiefziehblechen aus verschiedenen Materialien erprobt.
Tiefziehen mit dem Optimizer4D
Körperschall ist Träger von wichtigen Prozessinformationen – selbst schwache Signale können mit Hilfe der QASS-Technologie aus den Maschinengeräuschen extrahiert werden. Der Optimizer4D ermöglicht eine robuste und industrietaugliche Beurteilung des Produktionsprozesses durch eine schnelle Abtastrate, eine adaptive Filterung und innovative Mustererkennung. Langfristig ist eine nachgelagerte Prüfung nicht mehr notwendig, da während des Prozesses "zugehört" wird. Taktzeiten werden nicht beeinträchtigt. Der Vibrationssensor muss nicht zugestellt werden, sondern kann permanent an die Maschine angekoppelt werden und ermöglicht eine sofortige Ergebnisübermittlung mittels Profinet, Profibus oder SPS.
Schäden wie Risse oder Werkzeugschäden werden live sichtbar. Auch Produktionsfehler wie Ausdünnungen, Dopplungen oder Falten in Ihrem Tiefziehprozess können von unserer Messsoftware festgestellt werden.
Das Optimizer4D-Messsystem von QASS ist geeignet für die Prozessüberwachung, Monitoring tribologischer Effekte, Risserkennung und Tool Monitoring in vielen verschiedenen Industrieprozessen.
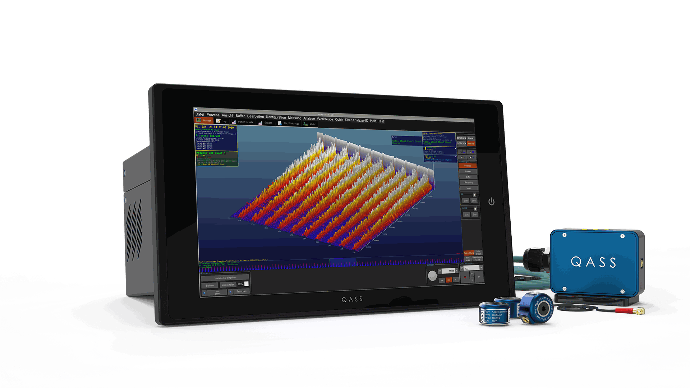
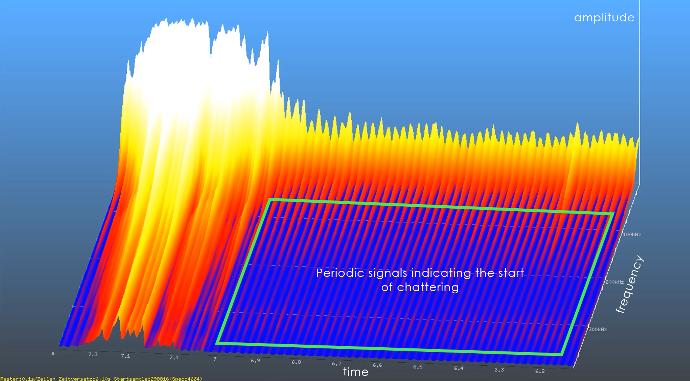
Messmethode Körperschall
Mittels Körperschallanalyse können wichtige Prozesssignale in Echtzeit erfasst werden. Unser Messsystem kann diese Signale evaluieren und entsprechend reagieren, um Ihren Prozess zu optimieren.
Jetzt Beratungstermin vereinbaren!
Informieren Sie sich unverbindlich bei unseren Experten über die Möglichkeiten für Ihre Industrieprozesse.