Aufgabe
Mit Hilfe von piezoelektrischen Sensoren wird die mehrstufige Querschnittreduktion eines Stahldrahtes in einer Trockenziehanlage überwacht. Dabei handelt es sich um eine Anlage, die aus mehreren Ziehsteinen (Umformung) unter Trockenschmierung (Tensid) besteht. Nach jeder Ziehstufe verfestigt sich der Draht (Kaltverfestigung). Dabei ändert sich das Reibverhalten erheblich. Das Ziehwerkzeug und die Schmiermittelversorgung müssen für jede Stufe neu angepasst werden. Im idealen Schmierungszustand herrscht Mischreibung. Diese lässt sich akustisch gegenüber Haft- oder Flüssigkeitsreibung unterscheiden.
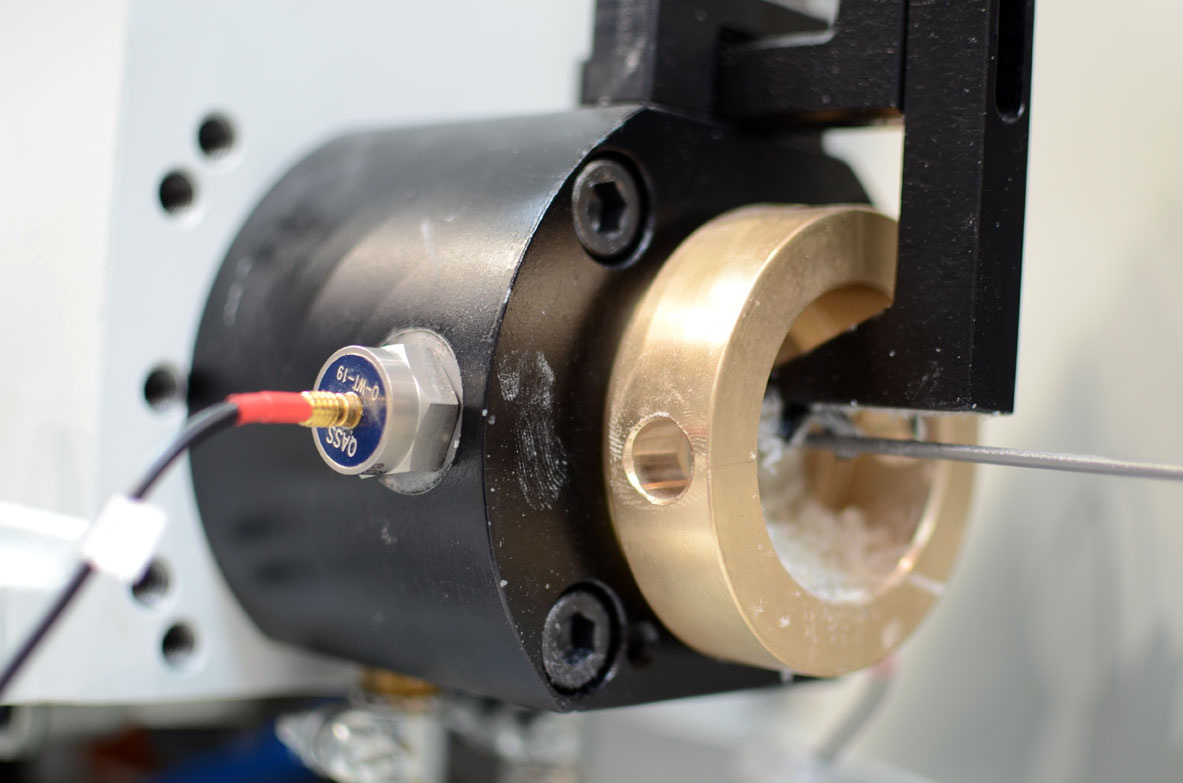
Abb. 1: SE-Sensor Applizierung am Ziehwerkzeuggehäuse.
Verfahren/Lösungsweg
Für die Inline-Detektion wird der Optimizer4D verwendet. Dabei handelt es sich um ein Messsystem, dass über eine FPGA basierte Messkarte verfügt. Damit ist auf bis zu vier Kanälen eine hohe Datenaufzeichnungsrate von bis zu 100 MB/Sek. möglich. Eine Kernfunktion ist eine Short-Time-Fourier-Transformation (STFT). Ein Zeit-Amplituden-Signal wird in den Frequenzbereich invertiert. Das Verfahren ist als Hoch-Frequenz-Impuls-Messung bekannt. Charakteristische Signale von Produktionsprozessen lassen sich physikalischen-werkstoffverändernden Prozessen wie Reibung, plastische Verformung und Risse zuordnen. Die Signalaufnahme erfolgt durch den verschraubten SE-Sensor am Ziehwerkzeuggehäuse (Abb. 1).
Zur Unterscheidung zwischen Stör- und Nutzsignalen werden elektronische Filter wie Frequenzmasken, dynamische Hüllkurven oder Hochpassfilter eingesetzt. Die Software setzt adaptiv und automatisch Frequenzhüllkurven. Dazu wird die Form der kontinuierlichen Signale vom Umformvorgang eingelernt und referenziert. Abweichungen der Signale können in verschiedene Toleranzstufen gesetzt werden.
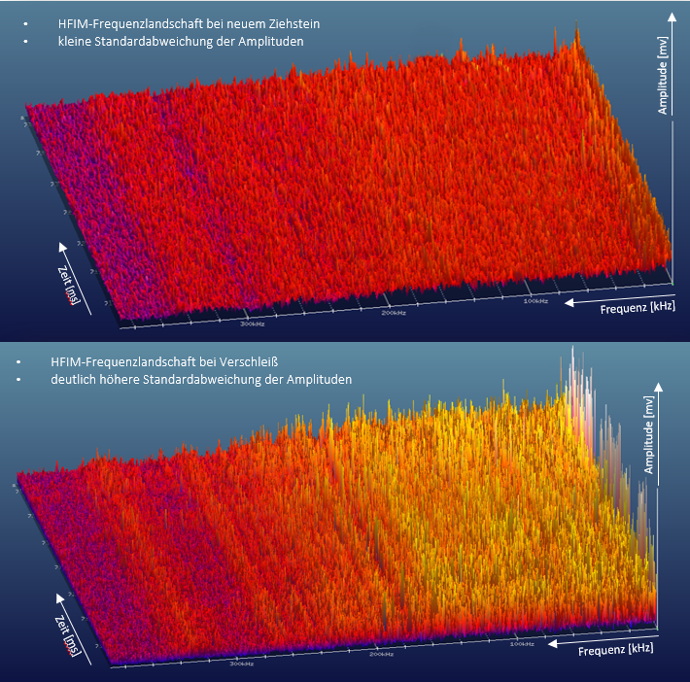
Abb. 2: Vergleich zwischen einem intakten Ziehwerkzeug (oben) und einem verschlissenen Ziehwerkzeug (unten).
Ergebnisse
Kontinuierlich werden Veränderungen im tribologischen System visualisiert, sodass kritische Reibleistungen am Werkzeug und am Draht vermieden werden. Mit zunehmendem Verschleiß emittiert das Werkzeug stärkere Signale. Die Abb. 2 zeigt, basierend auf der HFIM-Landschaft, ein Werkzeug zu Produktionsbeginn sowie den resultierenden Verschleiß nach 24 Stunden Dauereinsatz. Dabei ergibt die Ableitung aus der Summe einzelner Frequenzabweichung den Trend an (Abb. 3).
Sobald sich die tribologischen Verhältnisse kritisch verändern, ändert sich auch das HFIM-Signalabbild deutlich. Diesen Unterschied in der Systemreibungen detektiert Optimizer4D selbsttätig und automatisch.
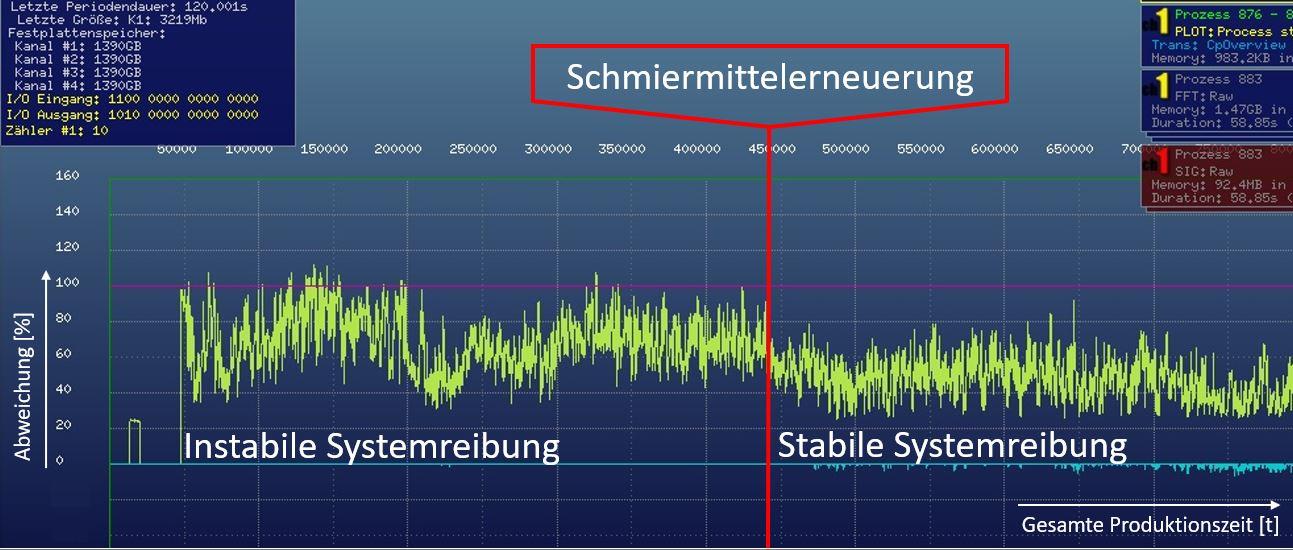
Abb. 3: Kontinuierlich werden Veränderungen im tribologischen System visualisiert, sodass kritische Reibleistungen am Werkzeug und am Draht vermieden werden.