Welding
Real-time evaluation of welding processes through acoustic monitoring
In-process monitoring
The permanent and friction-locked connection of the QASS acoustic sensor to the machine, enables the Optimizer4D to monitor your welding process without interruption. The data is processed and evaluated in real time.
Modular user interface
The QASS weld monitoring also benefits from a customizable user interface. Key process variables and data can be visualized at a glance, according to your preferences, making the Optimizer4D a self-sufficient and optimal monitoring system.
Non-destructive
The Optimizer4D monitors your welding process non-destructively. All process data are detected and recorded by means of a structure-borne sound sensor. Due to real-time data processing, the Optimizer4D enables you to optimize the cycle times.
Sensor fusion
To assess the quality of your welding even more effectively, the QASS weld monitoring offers three additional methods of data acquisition: additional monitoring of current/voltage, the inspection of the surfaces by means of line scanner, as well as the downstream inspection of the heat entry zone by QASS µmagnetics.
Real-time evaluation and error detection
In automated welding processes, it is currently hardly possible to detect sporadically occurring welding defects or process drifts that lead to defective weld seams in process and thus initiate suitable countermeasures in a timely manner.
The Optimizer4D detects and documents weak points and defects in the weld seam during the process.
With the help of state-of-the-art analysis technology, the system evaluates the weld seams based on their quality and classifies them according to correct, processable or irreparable defects. In this way, process faults such as stress cracks, weld pores, burn-through and binding defects can be reliably detected.
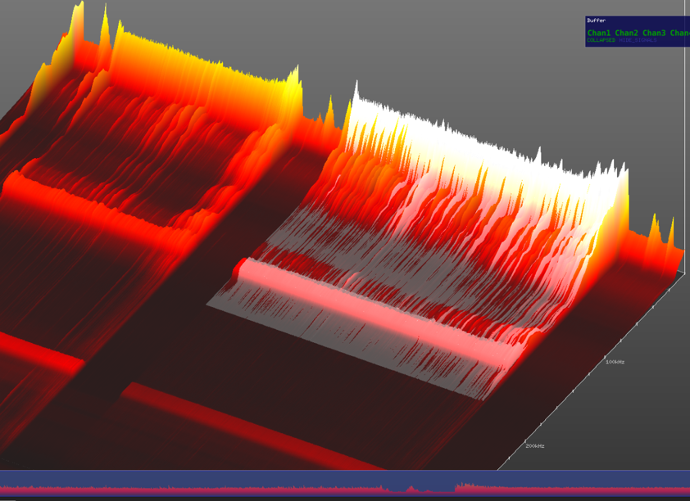
Evaluation using Envelope Surface Tool
- The enveloping surface object is activated at the beginning of the welding process.
- The enveloping surface object is calculated based on a statistically relevant number of OK processes.
- If a process deviates from the standard, the Optimizer4D detects the number and size of the deviations (punctures).
Connect multiple sources of information
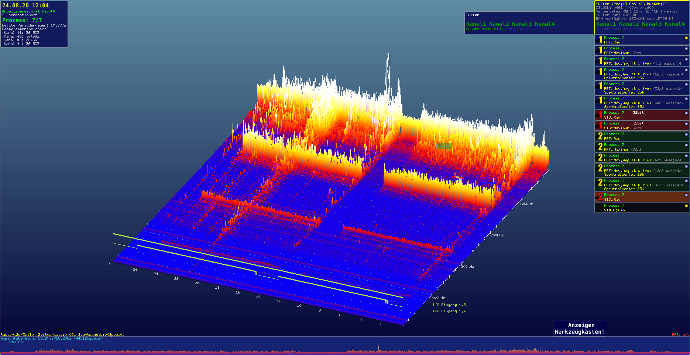
Structure-borne sound in welding
The QASS measuring system Optimizer4D works on the basis of structure-borne sound. Cold cracks, pore formation, or potentially incorrect welding parameters generate acoustic signal changes that are detectable by our measuring system at the moment of their occurrence.
The measurement signals are digitized by the Optimizer4D and transformed and processed in real time using Fast Fourier Transformation (FFT), so that they are immediately available to the QASS Software Analyzer4D. The results are clearly visualized in the QASS 3D spectral landscape.
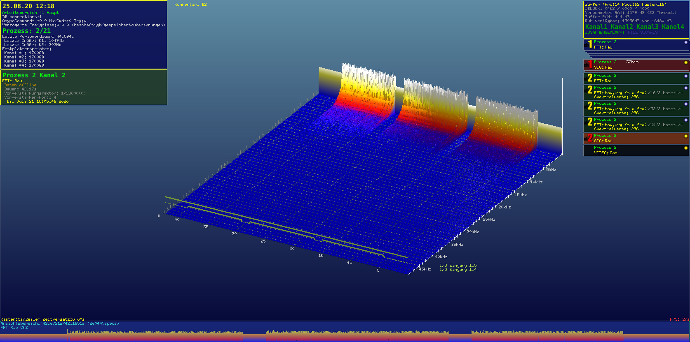
Current and voltage monitoring
For complete monitoring of the welding process, the Optimizer4D also measures the welding current and voltage of your welding system. QASS also applies the FFT and converts the amplitude-time signal of the welding current/voltage into an amplitude-frequency-time signal.
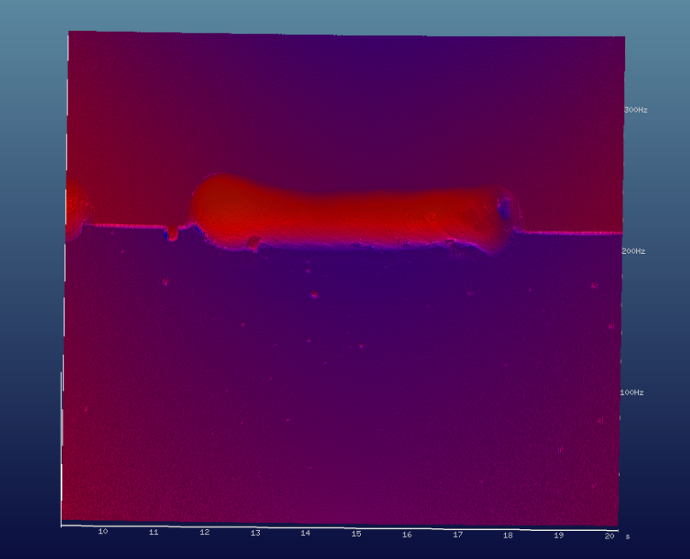
Measurement of welding seams by line scanner
In order to achieve even greater process precision, the weld seams are measured using a line scanner if necessary and prepared in a 3D representation. The QASS analysis tools can then assess defects such as burn-through, seam offset and much more based on the 3D shape of the weld seam.
These results are then automatically correlated with the results from HFIM, current/voltage and the micromagnetic measurement of the heat-affected zone, thus providing a very accurate picture of the quality.
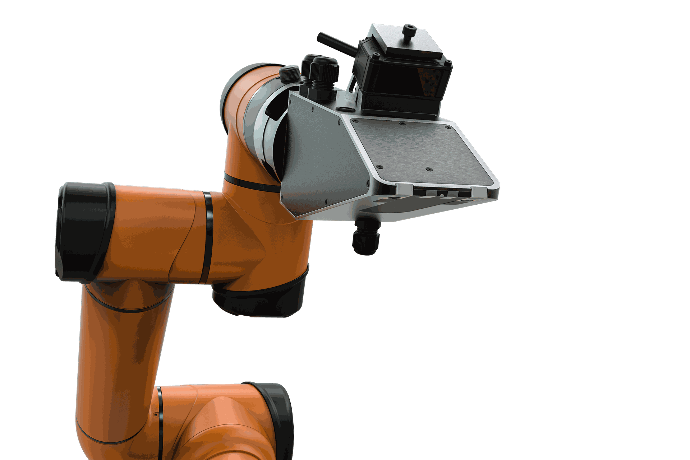
Testing the heat-affected zone
In the third step, in addition to our structure-borne sound measurement method, we can non-destructively inspect the heat-affected zone of suspect weld seams. The basis for this is the QASS QOBOT handling system and the QASS µmagnetic method, in which we can perform non-destructive hardness tests using Barkhausen noise.
Our references
Machine manufacturers offering QASS technology as a standard solution
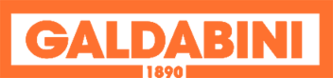
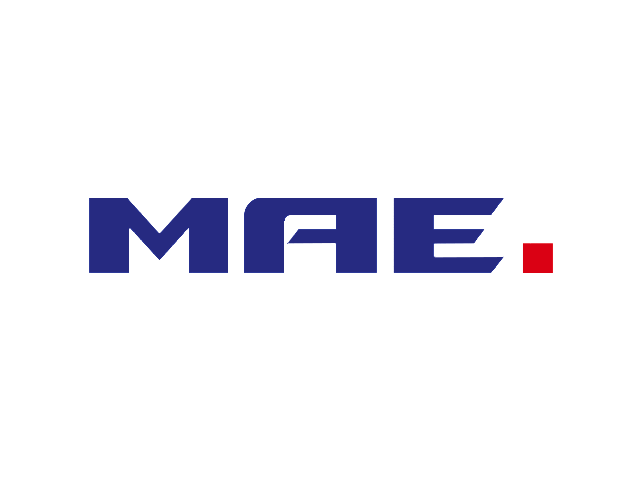
Arrange a consultation appointment now!
Ask our experts about the possibilities for your industrial processes without obligation.